[Precision ERW tube mill machinery]Enhancing Manufacturing Efficiency: An In-Depth Look at Precision ERW Tube Mill Machinery and Its Applications in Modern Industry
News 2024-7-26
In today’s fast-paced manufacturing environment, the demand for high-quality tubes and pipes has surged across various industries, including automotive, construction, and energy. As sectors increasingly move towards automation and precision in production processes, equipment designed for the efficient production of tubes has become crucial. Among these, Precision ERW (Electric Resistance Welded) tube mill machinery stands out as a key player in shaping the future of tube manufacturing.
**Understanding Precision ERW Tube Mill Machinery**
Precision ERW tube mill machinery is engineered for the production of welded tubes and pipes from hot or cold rolled steel strips. The precision aspect of such machinery refers not only to the dimensional accuracy of the tubes produced but also to the overall consistency in quality, surface finish, and mechanical properties. This machinery uses the electric resistance welding process, where heat generated from high-frequency electrical currents is applied to join the edges of the steel strip, producing a solid weld that can support a variety of end-use applications.
**The Process of Tube Production**
The fundamental process of tube production involves several steps, beginning with coil preparation. The steel strip is unwound, leveled, and fed into the mill, where it undergoes forming operations through a series of rollers. The mill geometry and the arrangement of forming stands are meticulously designed to achieve the desired tube profile, whether round, square, or rectangular.
Once the strip has been formed into a tube shape, it moves to the welding section of the machine. Here, the edges of the strip are heated through the resistance welding process, allowing them to fuse together upon contact. This rapid welding process is not only efficient but also retains the material’s structural integrity, making it ideal for a wide array of applications.
After welding, the tube undergoes several additional operations, including sizing, cutting, and finishing. Sizing ensures that the tube meets precise outer dimensions, while finishing may involve processes like deburring or applying protective coatings, further enhancing the tube's quality and performance characteristics.
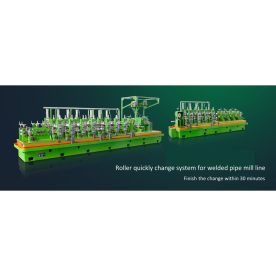
Enhancing Manufacturing Efficiency: An In-Depth Look at Precision ERW Tube Mill Machinery and Its Applications in Modern Industry
The advantages of using precision ERW tube mill machinery are manifold. Firstly, the precision aspect allows for tight tolerances in diameter and wall thickness, essential for industries where performance and safety are paramount. The consistency achieved through advanced automation minimizes waste and optimizes resource use, leading to cost savings for manufacturers.
Moreover, the speed with which these machines can operate amplifies productivity. Modern ERW tube mills can produce high volumes of tubes in a relatively short time frame, empowering manufacturers to meet increasing demand without compromising quality.

Enhancing Manufacturing Efficiency: An In-Depth Look at Precision ERW Tube Mill Machinery and Its Applications in Modern Industry
**Applications Across Industries**
The applications of precision ERW tubes are extensive. In the automotive industry, precision ERW tubes are used for exhaust systems, frames, and other structural components that require high strength and durability. In construction, these tubes find use in scaffolding and structural supports, where safety and reliability are critical. The energy sector utilizes precision ERW tubes in pipeline systems and various applications requiring resistance to high pressures and extreme conditions.

Enhancing Manufacturing Efficiency: An In-Depth Look at Precision ERW Tube Mill Machinery and Its Applications in Modern Industry
As we look towards the future, the focus on sustainability and energy efficiency in manufacturing processes is gaining momentum. Precision ERW tube mill manufacturers are continually innovating, integrating smart technologies such as IoT and AI into their machinery. Such innovations not only enhance productivity but also improve monitoring and control over the manufacturing process, contributing to lower energy consumption and reduced waste.
In conclusion, precision ERW tube mill machinery represents a crucial component in modern manufacturing, facilitating the production of high-quality tubes for various applications. Its benefits extend beyond mere efficiency, encompassing precision, versatility, and adaptability, thereby solidifying its role in meeting the evolving demands of industry. As technology continues to advance, the future of ERW tube manufacturing will undoubtedly be shaped by these innovations, ensuring sustainable practices while maintaining excellence in production standards.