[High frequency welder]Exploring the Advancements in High Frequency Welder Technology: Revolutionizing Modern Welding Techniques for Enhanced Efficiency
News 2024-7-26
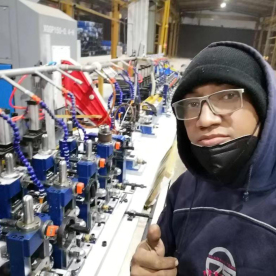
Exploring the Advancements in High Frequency Welder Technology: Revolutionizing Modern Welding Techniques for Enhanced Efficiency
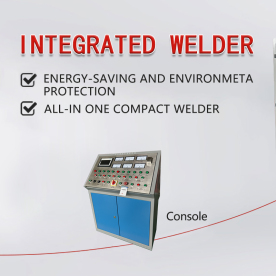
Exploring the Advancements in High Frequency Welder Technology: Revolutionizing Modern Welding Techniques for Enhanced Efficiency
High frequency welding, also known as high-frequency induction welding, utilizes high-frequency electromagnetic energy to create welds in metal components. This technique is especially prevalent in applications requiring the joining of materials like steel, stainless steel, and various alloys. Unlike traditional welding methods, which may apply intense heat over a wider area, high frequency welding focuses on a narrow zone, allowing for rapid heating and precise control over the welding process.
At the core of high frequency welding technology is its ability to generate localized heat through electromagnetic induction. By passing a high-frequency current through an inductor coil surrounding the workpieces, the materials experience rapid temperature elevation. This localized heating causes the edges of the metal parts to reach plasticity and ultimately bond together when sufficient pressure is applied. The result is a strong weld that can withstand significant stresses and operational demands.
One of the standout benefits of using a high frequency welder is its increased efficiency. Traditional welding methods can result in lengthy production times due to the cooling periods required between passes and the need to remove slag or other impurities from the weld area. High frequency welding minimizes these downtime concerns as it allows for continuous operation with minimal need for secondary processing. Furthermore, the speed of the setup and the quick transitions between welds lead to increased output, significantly boosting overall productivity.
Moreover, the precision offered by high frequency welders is unmatched. The localized heating process minimizes thermal distortion and warping, yielding aesthetically pleasing welds with exceptional integrity. This precision is particularly beneficial in applications where tight tolerances are essential, such as in automotive parts or aerospace components. Additionally, a high frequency welder produces less heat-affected zone (HAZ), reducing the risk of material degradation or loss of fatigue resistance in the welded joint.
The applications of high frequency welding are wide-ranging. It is commonly employed in industries such as automotive, aerospace, electronics, and pipe manufacturing. In the automotive sector, for instance, high frequency welders are utilized to join exhaust systems, fuel tanks, and other critical components requiring robust and reliable welds. In electronics, this technology is often used for creating high-frequency inductive components such as transformers and inductors, where connection integrity is paramount.
Despite its many advantages, high frequency welding technology does require careful evaluation and investment. The initial costs associated with acquiring a high frequency welder and the expertise needed to operate it can be significant. Nevertheless, for manufacturers aiming to enhance their production capabilities, the long-term benefits—through improved throughput, reduced material wastage, and higher quality output—often justify these initial expenditures.
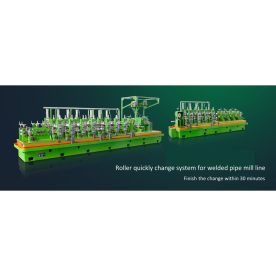
Exploring the Advancements in High Frequency Welder Technology: Revolutionizing Modern Welding Techniques for Enhanced Efficiency
In conclusion, high frequency welders represent a significant leap forward in welding technology, offering distinct advantages in terms of efficiency, precision, and versatility. As industries continue to seek ways to optimize their operations and innovate their production processes, the adoption of high frequency welding is poised to grow. For manufacturers committed to achieving superior quality and performance in their welding applications, harnessing the power of high frequency welding technology may be the key to maintaining a competitive edge in an ever-evolving marketplace.