[Industrial Cold Cutting Saw Machine]Transforming Metal Fabrication: The Indispensable Role of Industrial Cold Cutting Saw Machines in Modern Manufacturing Processes
News 2024-7-26
In the highly competitive world of metal fabrication, precision and efficiency are essential for maintaining a competitive edge. One of the most critical tools in achieving these objectives is the Industrial Cold Cutting Saw Machine. These machines have revolutionized the metalworking industry by providing an efficient, accurate, and versatile solution for cutting various materials, including steel, aluminum, and other alloys. This article explores the features, benefits, and applications of industrial cold cutting saw machines, highlighting their significance in contemporary manufacturing processes.
What is an Industrial Cold Cutting Saw Machine?
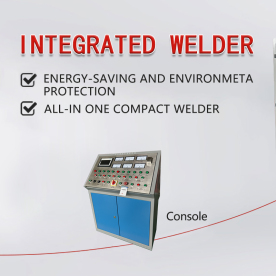
Transforming Metal Fabrication: The Indispensable Role of Industrial Cold Cutting Saw Machines in Modern Manufacturing Processes
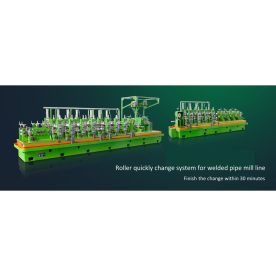
Transforming Metal Fabrication: The Indispensable Role of Industrial Cold Cutting Saw Machines in Modern Manufacturing Processes
1. **High Precision and Accuracy**: Industrial cold cutting saw machines are engineered to offer exceptional cutting accuracy. Most models feature advanced digital controls that allow users to set precise angles and dimensions, ensuring that every cut is consistent and reliable. This level of precision is essential for components that require tight tolerances, especially in industries such as automotive, aerospace, and construction.
2. **Versatility**: These machines can handle a wide variety of materials and thicknesses. From solid bars to pipes and profiles, cold cutting saws are adaptable to different job requirements, making them an invaluable asset in various manufacturing sectors.
3. **Improved Surface Finish**: By cutting without generating heat, the cold cutting saw provides a superior surface finish. This eliminates the need for extensive post-cut processing, such as deburring or polishing, saving time and labor costs.
4. **Reduced Waste**: The precision of these machines results in minimal material waste. With high-quality cuts and the ability to follow intricate shapes, manufacturers can optimize their material utilization, leading to cost savings.
5. **Operator Safety and Ergonomics**: Modern cold cutting saw machines prioritize operator safety. Many models come equipped with safety features such as blade guards, emergency stop buttons, and automatic shut-offs. Additionally, ergonomic designs help reduce operator fatigue, enhancing productivity during long shifts.
Benefits of Using Industrial Cold Cutting Saw Machines

Transforming Metal Fabrication: The Indispensable Role of Industrial Cold Cutting Saw Machines in Modern Manufacturing Processes
2. **Lower Operational Costs**: Although the initial investment in an industrial cold cutting saw machine may be higher than that of traditional saws, the long-term operational savings are significant. Reduced waste material, lower tooling costs due to longer blade life, and decreased energy consumption contribute to overall cost efficiency.
3. **Improved Quality Control**: The ability to achieve consistent, high-quality cuts minimizes the chances of defects and rework. Businesses can maintain higher standards of quality control, leading to better customer satisfaction and fewer returns or complaints.
4. **Sustainability**: Cold cutting processes generate less scrap and waste, contributing to more sustainable manufacturing practices. Companies are increasingly focusing on eco-friendly methods, and industrial cold cutting saw machines can play a vital role in achieving these goals.
Applications in Various Industries
Industrial cold cutting saw machines find their applications across a diverse array of industries. In the automotive sector, they are essential for preparing parts such as frames and structural components. In construction, cold cutting saws are utilized for cutting steel beams, pipes, and various profiles. Additionally, the aerospace industry employs these machines for producing high-precision components that meet strict regulatory standards. The versatility and efficiency of cold cutting saws make them valuable tools in metalworking, construction, manufacturing, and beyond.
Conclusion
In a landscape where efficiency, precision, and adaptability are paramount, industrial cold cutting saw machines have emerged as essential equipment for modern manufacturing processes. Their ability to deliver high-quality cuts, minimize waste, and enhance safety makes them a smart investment for any company engaged in metal fabrication. As industries continue to evolve and demand for precision increases, the role of industrial cold cutting saw machines will only become more vital in shaping the future of manufacturing.