[High frequency welder for metal]Understanding the Role of High Frequency Welders for Metal Fabrication in Modern Manufacturing Processes
News 2024-7-26
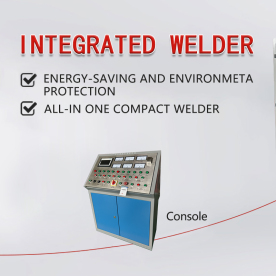
Understanding the Role of High Frequency Welders for Metal Fabrication in Modern Manufacturing Processes
High frequency welders for metal have revolutionized the way metal components are joined in various industries, providing not only efficiency but also precision and strength. The significance of welding as a fabrication method cannot be overstated, especially in sectors such as automotive, aerospace, construction, and manufacturing. With advancements in technology, the availability of high frequency welding systems has been a game changer, enabling manufacturers to achieve higher quality welds in less time compared to traditional welding methods.
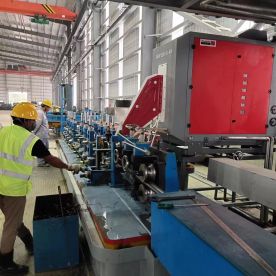
Understanding the Role of High Frequency Welders for Metal Fabrication in Modern Manufacturing Processes
One of the most notable applications of high frequency welders for metal is in the production of pipes and tubing. In industries such as oil and gas, the demand for high-quality, durable piping systems is paramount. These pipes must not only withstand high pressures but also corrosion and fatigue over time. High frequency welding ensures that the seams of these pipes are consistently strong, minimizing the risk of failure. The speed of the welding process also increases production rates, allowing businesses to meet tight deadlines and growing market demands.
Another key advantage of high frequency welding is its ability to join dissimilar metals. With the right techniques and equipment, manufacturers can weld materials with different electrical and thermal properties, expanding the range of applications for their products. This capability is particularly beneficial in industries that require lightweight and strong materials, such as aerospace, where components made from aluminum and titanium need to be securely joined without adding excessive weight.
The technology behind high frequency welders for metal has also been instrumental in improving safety standards. Traditional welding methods frequently produce harmful gases and fumes, which can pose health risks to operators. Conversely, high frequency welding often generates fewer toxic byproducts, making it a safer option in poorly ventilated environments. Additionally, the faster welding times reduce the overall exposure to heat, which helps maintain the integrity of the materials being joined and minimizes distortion.
In addition to these benefits, the precision of high frequency welding plays a critical role in modern manufacturing processes. The ability to control heat input with high accuracy means that sensitive components can be welded without the risk of over-heating or under-heating. This level of control ensures that welds are consistent and meet stringent quality standards. Manufacturers today are often mandated to adhere to rigorous specifications; thus, using high frequency welding technology allows them to remain compliant and competitive in the marketplace.
Despite its many advantages, it’s important to understand the operational demands of high frequency welders for metal. Operators must be thoroughly trained to understand the nuances of the equipment, as improper use can lead to defects in the welds or damage to the machinery. Consistent maintenance and calibration of the machines are also critical to ensure optimal performance and longevity of the equipment.
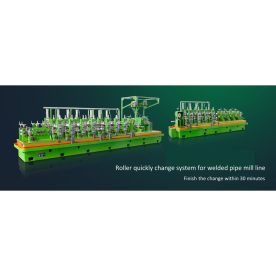
Understanding the Role of High Frequency Welders for Metal Fabrication in Modern Manufacturing Processes
In conclusion, high frequency welders for metal stand at the forefront of welding technology, providing manufacturers with the tools necessary to produce robust, high-quality welds efficiently. Their role in modern fabrication processes is indispensable, allowing industries to meet growing demands while adhering to strict safety and quality standards. As technology continues to advance, the potential applications and benefits of high frequency welding will likely expand, solidifying its place as a vital component in the future of manufacturing.