[Customized Spare Parts for Tube Mills]Enhancing Efficiency and Reducing Downtime: The Importance of Customized Spare Parts for Tube Mills in Modern Manufacturing
News 2024-7-26
In the fast-paced world of modern manufacturing, efficiency and reliability are paramount. For many industries reliant on tube mills, the quest for perfection in the production process hinges on high-quality machinery and components. One of the most effective ways to ensure optimum functionality in tube mills is through the utilization of customized spare parts. With precision engineering and tailored solutions, these parts play a critical role in reducing downtime, enhancing performance, and ultimately driving profitability in manufacturing operations.
Understanding Tube Mills
Tube mills are essential for shaping and forming metal into tubular products used in a myriad of applications, from automotive components to construction materials. These complex machines work under demanding conditions, requiring not only precision but also durability. Tube mills consist of multiple components, including rollers, bearings, and cutting mechanisms, which must meet stringent specifications to function effectively.
As tube mills operate continuously, wear and tear are inevitable. The need for spare parts arises from regular maintenance and the occasional unexpected breakdown. However, not all spare parts are created equal. Off-the-shelf components may seem convenient, but they often come with limitations. This is where the importance of customized spare parts becomes apparent.
The Role of Customized Spare Parts
Customized spare parts for tube mills are designed with specific requirements in mind, addressing the unique challenges faced by individual machines. These bespoke components can provide a multitude of benefits:
1. **Enhanced Compatibility**: Customized spare parts are engineered to fit the exact specifications of the existing machinery. This ensures seamless integration, reducing the chances of operational inefficiencies that can occur with generic parts.
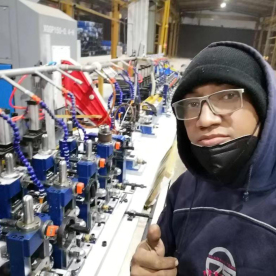
Enhancing Efficiency and Reducing Downtime: The Importance of Customized Spare Parts for Tube Mills in Modern Manufacturing
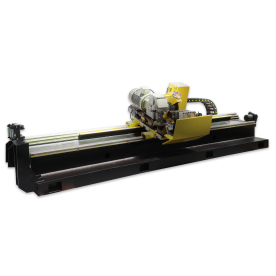
Enhancing Efficiency and Reducing Downtime: The Importance of Customized Spare Parts for Tube Mills in Modern Manufacturing
4. **Reduced Downtime**: One of the most significant advantages of using customized spare parts is the reduction in downtime. When businesses can quickly replace damaged components with parts that fit perfectly, operations can resume faster, minimizing disruptions and lost productivity.
5. **Tailored Solutions for Unique Challenges**: Every production line has its challenges, whether it’s due to the type of material being processed or the operational environment. Customized spare parts can address these particular issues, allowing companies to optimize their processes according to their unique needs.
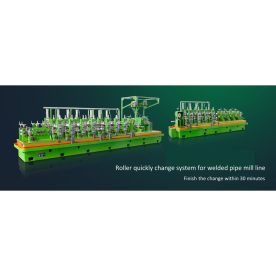
Enhancing Efficiency and Reducing Downtime: The Importance of Customized Spare Parts for Tube Mills in Modern Manufacturing
Creating customized spare parts for tube mills involves several key steps:
1. **Assessment of Needs**: It starts with a comprehensive assessment of the existing machinery and the specific requirements. This may involve consultations with engineers and technicians to understand the challenges faced and the desired outcomes.
2. **Design and Engineering**: Once the needs are identified, custom designs are developed. This may include CAD modeling and simulations to ensure that the parts will meet performance specifications.
3. **Material Selection**: Selecting the right materials is critical to the performance and durability of the parts. Factors like abrasion resistance, thermal properties, and strength must be considered.
4. **Manufacturing and Quality Control**: The manufacturing process involves precision machining, fabrication, and assembly, followed by stringent quality control measures to ensure that each part meets the required standards.
5. **Installation and Testing**: Finally, the customized spare parts are installed on the tube mills, followed by rigorous testing to confirm their efficacy.
Conclusion
In an era where every second counts in production, the strategic choice of using customized spare parts for tube mills cannot be overstated. By investing in tailored solutions, manufacturers can enhance the efficiency and longevity of their operations, leading to greater overall productivity and profitability. Customized spare parts are not just replacements; they are essential components in a well-oiled manufacturing machine that can adapt to meet the demands of modern industry. As the market continues to evolve, the integration of customized solutions will be integral to staying competitive and successful in the manufacturing landscape.