[High frequency welder for plastic]Exploring the Advantages and Applications of High Frequency Welders for Plastic in Modern Manufacturing
News 2024-7-24
In today’s fast-paced manufacturing world, the need for efficient, reliable, and high-quality joining methods is critical, especially in the plastic industry. One of the most innovative and effective techniques to achieve this is the use of high frequency welders for plastic. This advanced technology has significantly transformed how plastic materials are bonded together, providing numerous advantages over traditional welding methods. In this article, we will explore the functions, benefits, and applications of high frequency welders for plastic, highlighting their importance in modern manufacturing processes.
High frequency welding, also known as radio frequency (RF) welding, is a process that uses electromagnetic energy to heat and bond plastic materials. This technique is particularly suitable for thermoplastic materials, which become soft and pliable when exposed to heat. The high frequency welders generate electromagnetic waves that cause the molecules in the plastic to vibrate, producing heat at the interface of the materials being joined. This localized heating allows for quick and efficient welding, resulting in strong, durable bonds without the need for additional adhesives or mechanical fasteners.
One of the standout advantages of high frequency welders for plastic is their speed. The welding process is incredibly fast, typically taking just a few seconds to complete. This speed not only enhances productivity in manufacturing environments but also reduces the overall production cycle time. Traditional welding methods, on the other hand, can be slow and labor-intensive, leading to higher costs and inefficiencies. With high frequency welding, manufacturers can produce larger quantities of products in shorter periods, ensuring they meet market demand swiftly.
Another critical benefit of high frequency welders is the quality of the welds they produce. The localized heating minimizes the risk of damaging surrounding materials, ensuring that the finished products maintain their structural integrity and appearance. High frequency welding creates clean and seamless joints, which are essential for many applications, especially those requiring aesthetic considerations. Additionally, the strong bond formed during the process results in high tensile strength, making the products more durable and reliable for practical use.
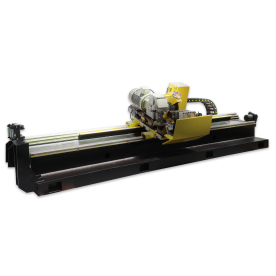
Exploring the Advantages and Applications of High Frequency Welders for Plastic in Modern Manufacturing
The design of high frequency welders is often another attractive feature for manufacturers. Many modern machines come with programmable settings, enabling operators to adjust parameters such as temperature, pressure, and welding time to match the specific requirements of different materials. This level of customization ensures optimal results and enables manufacturers to cater to varying project demands without needing extensive reconfiguration.
In addition to the manufacturing benefits, high frequency welders are also more environmentally friendly compared to some traditional welding techniques. Since they do not require the use of solvents, adhesives, or other harmful substances, they contribute to a reduction in volatile organic compounds (VOCs) being emitted into the atmosphere. This eco-friendly aspect aligns with the growing trend in industries seeking sustainable manufacturing practices.
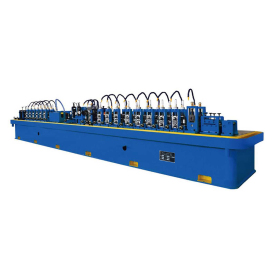
Exploring the Advantages and Applications of High Frequency Welders for Plastic in Modern Manufacturing

Exploring the Advantages and Applications of High Frequency Welders for Plastic in Modern Manufacturing
In conclusion, high frequency welders for plastic represent a significant advancement in the field of manufacturing. Their speed, quality of welds, versatility, and eco-friendly attributes make them an essential tool for companies seeking to optimize their production processes and maintain high standards of quality. As industries continue to evolve and embrace new technologies, high frequency welders will undoubtedly remain a key component in the ongoing quest for efficiency and excellence in plastic manufacturing.