[Customized ERW tube mill solutions]Innovative Customized ERW Tube Mill Solutions: Empowering the Future of Metal Fabrication and Manufacturing
News 2024-7-24
In the modern landscape of metal fabrication and manufacturing, the ability to produce high-quality products efficiently and cost-effectively is paramount. One of the most critical components of this industry is the Electric Resistance Welded (ERW) tube mill, an essential machine for creating welded tubes from coiled steel. With technological advancements and increased industry demands, the need for customized ERW tube mill solutions has never been greater. Such tailored solutions not only enhance productivity but also ensure that manufacturers can meet diverse market needs and maintain a competitive edge.
The ERW tube mill process involves several stages, including forming, welding, sizing, and cutting. Each of these stages must be meticulously engineered to produce tubes that meet specific industry standards and customer requirements. This is where customized ERW tube mill solutions come into play. Unlike standard machinery, customized solutions allow for adjustments in design, specifications, and functionality based on the unique needs of the client.
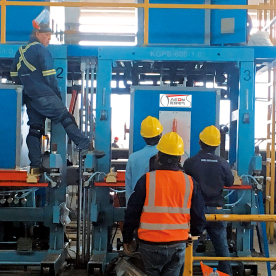
Innovative Customized ERW Tube Mill Solutions: Empowering the Future of Metal Fabrication and Manufacturing
1. **Enhanced Production Efficiency:** Custom ERW tube mills can be tailored to accommodate various production rates, ensuring that manufacturers can meet demand without compromising quality. By optimizing the machinery’s setup and production parameters, companies can reduce downtime, increase throughput, and streamline their operations.
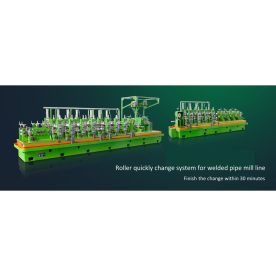
Innovative Customized ERW Tube Mill Solutions: Empowering the Future of Metal Fabrication and Manufacturing
3. **Improved Quality Control:** Custom solutions can incorporate advanced technologies like automated quality monitoring systems, which can identify defects in real-time during the production process. This leads to higher quality end-products and reduced waste, ultimately improving the bottom line.
4. **Cost-Effectiveness:** While the initial investment in customized equipment may be higher than that of standard machinery, the long-term savings realized through reduced operational costs, improved efficiency, and enhanced product quality often outweigh the upfront expenses. Custom ERW tube mills can be designed to minimize energy consumption and raw material waste, further contributing to cost-effectiveness.
5. **Increased Flexibility and Scalability:** As market demands change, manufacturers must be able to adapt quickly. Customized ERW tube mills can be designed with modular components, allowing for easy upgrades or modifications as needed. This scalability ensures that companies can remain agile and responsive to shifting market conditions.
The Process of Developing Customized ERW Tube Mill Solutions
Creating a customized ERW tube mill solution begins with an in-depth consultation between the manufacturer and the equipment supplier. This collaborative approach ensures that the supplier understands the specific needs and challenges faced by the manufacturer. Key factors considered during this phase include:
- **Material Specifications:** Different materials require different processing techniques. Custom solutions can be designed to handle a wide range of materials, including carbon steel, stainless steel, and alloy steel.
- **Tube Specifications:** The intended application of the tubes dictates their size, shape, and wall thickness. Understanding these requirements is crucial for developing effective solutions.
- **Production Volume:** Knowledge of the required output helps in engineering an appropriate tube mill design, balancing speed and quality.
- **Automation and Technology:** Incorporating the latest technologies, including Industry 4.0 elements like IoT connectivity and advanced robotics, can significantly enhance the performance of customized ERW tube mills.

Innovative Customized ERW Tube Mill Solutions: Empowering the Future of Metal Fabrication and Manufacturing
Numerous companies across various industries have benefited from investing in customized ERW tube mill solutions. For example, a leading automotive parts manufacturer sought to increase production capacity while reducing defect rates. By collaborating with a manufacturer of ERW tube mills, they implemented a tailored solution that included automated quality checks and a redesign of the welding process. As a result, the company not only increased its production efficiency by over 30% but also achieved a substantial reduction in waste and defects.
Conclusion
In an ever-evolving manufacturing landscape, the demand for high-quality, efficient, and flexible solutions remains crucial. Customized ERW tube mill solutions address these needs, empowering manufacturers to push the boundaries of productivity, quality, and innovation. As the industry continues to grow, embracing the power of customization in ERW tube mills will undoubtedly play a pivotal role in shaping the future of metal fabrication and manufacturing. By investing in tailored solutions, companies can ensure that they remain competitive while meeting the diverse needs of their customers.