[Pipe mill production line]Exploring the Advancements and Efficiency of Modern Pipe Mill Production Lines in the Manufacturing Industry
News 2024-7-23
The manufacturing industry has experienced significant advancements over the years, especially with the evolution of production lines that focus on creating high-quality products efficiently. One such innovation is the pipe mill production line, a sophisticated system designed for the mass production of pipes made from various materials such as steel, aluminum, and plastic. In this article, we delve into the intricacies of pipe mill production lines, including their components, operational processes, technological advancements, and the benefits they bring to the industry.
Understanding Pipe Mill Production Lines
A pipe mill production line encompasses a series of machinery and equipment specifically tailored for the fabrication of pipes. These lines utilize a combination of techniques, including welding, rolling, and stretching, to create pipes of different sizes and specifications. The types of pipes produced can vary widely—from seamless pipes used in oil and gas industries to welded pipes commonly found in construction and infrastructure projects.
Components of a Pipe Mill Production Line
A typical pipe mill production line consists of several essential components:
1. **Pipe Forming Machine**: This is the primary equipment where flat sheets or strips of metal are transformed into cylindrical shapes. The forming machine uses specialized rolls that gradually bend the material into a tube.
2. **Welding Equipment**: After the metal forms into a pipe shape, the seam must be welded to create a continuous structure. Modern pipe mills often employ high-frequency induction welding or TIG (Tungsten Inert Gas) welding methods to ensure strong and durable welds.
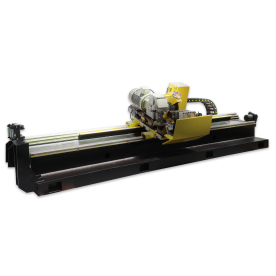
Exploring the Advancements and Efficiency of Modern Pipe Mill Production Lines in the Manufacturing Industry
4. **Cutting System**: After sizing, the continuous lengths of pipes require cutting to specified lengths. This is typically done using high-speed saws that can handle a range of pipe sizes.
5. **Finishing Equipment**: Finally, pipes may go through finishing processes, including coating or galvanizing, before packaging. This ensures enhanced durability and resistance to corrosion.
Operational Process: From Raw Material to Finished Product
The pipe production journey begins with the selection of high-quality raw materials, which are typically in coil form. The process commences with the uncoiling of the metal sheets, followed by the forming and welding stages. The entire production cycle can be automated, enhancing productivity while minimizing human error.
As the pipes move through the various stages—forming, welding, sizing, cutting, and finishing—quality control is paramount. Advanced inspection systems, including ultrasonic testing and x-ray inspection, are often employed to detect any flaws in the welds or structure.
Technological Advancements in Pipe Mill Production Lines
Recent years have seen the introduction of advanced technologies within pipe mill production lines. Automation, robotics, and smart manufacturing systems are transforming traditional methods, offering substantial benefits such as:
1. **Increased Efficiency**: Automation reduces the cycle time from raw material to finished product, enabling manufacturers to meet rising demands without sacrificing quality.
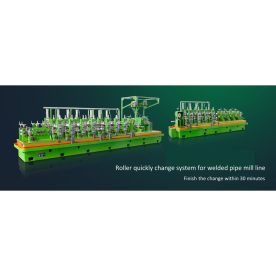
Exploring the Advancements and Efficiency of Modern Pipe Mill Production Lines in the Manufacturing Industry
3. **Data-Driven Insights**: Integrating IoT (Internet of Things) technologies allows manufacturers to collect and analyze data throughout the production process. This provides valuable insights for optimizing performance and reducing waste.
Benefits of Pipe Mill Production Lines
Implementing modern pipe mill production lines can yield numerous benefits for manufacturers, including:

Exploring the Advancements and Efficiency of Modern Pipe Mill Production Lines in the Manufacturing Industry
- **Scalability**: Modern production lines can easily adapt to changes in demand, whether through increased production speed or the ability to switch between different pipe sizes.
- **Sustainability**: Newer technologies promote energy efficiency and reduce waste, aligning with global sustainability goals and standards.
In conclusion, pipe mill production lines are at the forefront of manufacturing technology, enabling industries to efficiently produce high-quality pipes for a variety of applications. As advancements continue to shape this field, manufacturers stand to benefit from improved processes, reduced costs, and a stronger competitive edge in the global market. The future of pipe manufacturing looks promising, with innovation paving the way for even greater efficiencies and capabilities in pipe mill production.