[High frequency welder for plastic]Exploring the Advantages and Applications of High Frequency Welder for Plastic in Modern Manufacturing Processes
News 2024-7-23
In the ever-evolving landscape of manufacturing, the demand for innovative solutions that enhance efficiency, reduce costs, and ensure high-quality outputs continues to grow. Among the remarkable advancements in this field is the high frequency welder for plastic, a tool that has revolutionized the way thermoplastics are bonded and shaped. This article aims to delve into the functionalities, advantages, and wide-ranging applications of high frequency welding technology for plastic materials, shedding light on its significance in contemporary industrial settings.
Understanding High Frequency Welding
High frequency welding, also known as radio frequency (RF) welding or dielectric welding, involves using electromagnetic energy to generate heat within materials that contain polar molecules, such as plastics. This process ensures precise targeting of the welding area, enabling efficient bonding without negatively impacting the surrounding material. High frequency welders can deliver a spectrum of energies depending on the chosen frequency, typically ranging from 13.56 MHz to 40.68 MHz. This method is particularly effective for materials such as PVC, PU, and EVA, commonly used in various industrial applications.
The Benefits of Using a High Frequency Welder for Plastic
1. **Speed and Efficiency**: One of the most significant advantages of using high frequency welders is their rapid operation. The process can complete welds within seconds, making it ideal for high-volume production environments. This efficiency translates to increased productivity and lower operational costs.
2. **Strong and Durable Seams**: High frequency welded seams are known for their strength and durability. The process creates molecular bonds that can withstand considerable stress, making it suitable for products that must endure harsh conditions.
3. **Versatility**: High frequency welding is adaptable to various applications, from automotive parts to medical devices and consumer goods. This versatility means that companies can consolidate their manufacturing processes by employing a single technology for multiple applications.
4. **Precision**: High frequency welders allow for highly accurate control over the welding process, reducing the chances of defects and ensuring consistent quality in production. This precision is crucial, especially in industries where tolerances are critical.
5. **Environmentally Friendly**: The high frequency welding process generates minimal waste compared to traditional welding methods. Since the approach does not require additional bonding agents or adhesives, it promotes a more environmentally sustainable manufacturing practice.
Applications of High Frequency Welding in Various Industries
The high frequency welder for plastic finds its usage in diverse industries due to its unique capabilities. Here are some notable applications:
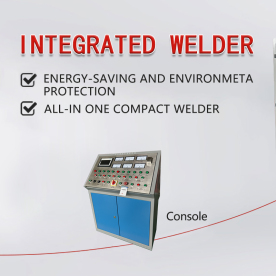
Exploring the Advantages and Applications of High Frequency Welder for Plastic in Modern Manufacturing Processes
2. **Medical Devices**: In the medical field, precision is paramount. High frequency welding is employed in manufacturing a variety of medical devices, including IV bags, catheters, and sterile packaging. The process ensures that medical products are safe, reliable, and compliant with stringent regulations.
3. **Consumer Goods**: Many items that consumers use daily, such as inflatable products, waterproof bags, and electronic device casings, utilize high frequency welding. The technology’s ability to create hermetic seals makes it perfect for products that require protection from dust and moisture.
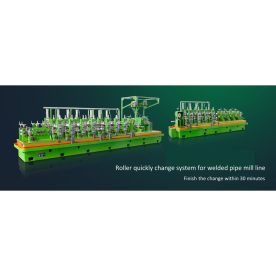
Exploring the Advantages and Applications of High Frequency Welder for Plastic in Modern Manufacturing Processes
5. **Packaging Solutions**: High frequency welding is increasingly being adopted in the packaging industry to create durable bags and pouches. Its efficiency in producing hermetically sealed packages is advantageous for food preservation and other sensitive products.

Exploring the Advantages and Applications of High Frequency Welder for Plastic in Modern Manufacturing Processes
The high frequency welder for plastic stands as a cornerstone of modern manufacturing practices. Its speed, efficiency, and versatility make it a preferred method for joining thermoplastic materials across various industries. As manufacturers continue to seek solutions that optimize production processes while maintaining quality standards, the role of high frequency welding is only set to grow. By investing in such technologies, companies can not only improve their operational capabilities but also contribute to a more sustainable future in manufacturing.