[Industrial-grade All-in-one Welder]Explore the Versatility and Efficiency of an Industrial-Grade All-in-One Welder for Your Manufacturing Needs
News 2024-7-23
In the fast-paced world of manufacturing and industrial fabrication, efficiency and versatility are paramount. An industrial-grade all-in-one welder offers the perfect solution for businesses looking to streamline their welding processes while maintaining high standards of quality and safety. These advanced machines combine multiple welding functions—such as MIG, TIG, and Stick welding—into a single unit, allowing for a seamless transition between processes and reducing the need for multiple standalone machines. In this article, we will delve into the features, benefits, and potential applications of an industrial-grade all-in-one welder.
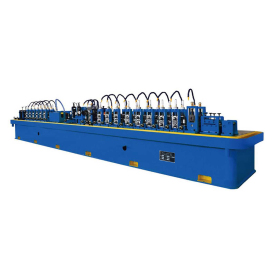
Explore the Versatility and Efficiency of an Industrial-Grade All-in-One Welder for Your Manufacturing Needs
Industrial-grade all-in-one welders are designed for heavy-duty applications and are engineered to withstand the rigors of workshop environments. Unlike traditional welders that serve a single purpose, these machines integrate various welding techniques into one cohesive system. This multifunctionality allows operators to tackle diverse tasks without the hassle of changing equipment or setups constantly.
A typical industrial-grade all-in-one welder is built with durable materials to ensure longevity and reliability. They come equipped with user-friendly interfaces and advanced technology that allows for precise control over welding parameters. Features like adjustable amperage, voltage control, and digital displays make it easy for welders to customize their settings for different materials and thicknesses.
Benefits of Using an All-in-One Welder
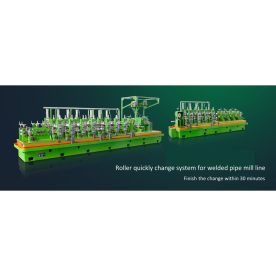
Explore the Versatility and Efficiency of an Industrial-Grade All-in-One Welder for Your Manufacturing Needs
2. **Versatility**: With the ability to perform different types of welding, an all-in-one welder is invaluable in dynamic environments where projects vary frequently. From sheet metal fabrication to pipe welding, these machines accommodate a wide range of materials, including steel, aluminum, and stainless steel. The capability to switch between MIG, TIG, and Stick welding on the fly increases workflow efficiency and offers flexibility in handling diverse projects.
3. **Time-Saving**: Time is money in the industrial sector. All-in-one welders are designed to minimize downtime by allowing operators to quickly transition between welding processes. The integrated systems reduce the lead time needed to set up equipment, which can significantly boost productivity on the shop floor.
4. **Enhanced Safety Features**: Modern industrial-grade welders come with numerous safety features that help protect both the operator and the equipment. These may include advanced cooling systems, automatic shut-off functions, and protective casings that minimize exposure to harmful weld fumes. Investing in a high-quality welder not only enhances productivity but also prioritizes the safety and well-being of your workforce.
Applications in Various Industries
Industrial-grade all-in-one welders are indispensable in numerous sectors, including:
- **Manufacturing**: Used extensively for assembly lines and production facilities, where different welding techniques may be required for different components. - **Construction**: From metal frameworks to structural components, these welders can handle varying thicknesses and materials commonly found in construction projects. - **Automotive**: In car manufacturing and repair operations, the ability to switch between welding methods quickly is crucial for maintaining efficiency on the assembly line. - **Shipbuilding**: The maritime industry greatly benefits from the versatility of all-in-one welders, as they can seamlessly adapt to various tasks—from hull fabrication to interior fittings.
Conclusion
