[Industrial tube making machinery]Exploring the Advances in Industrial Tube Making Machinery: Revolutionizing Manufacturing Processes for a Sustainable Future
News 2024-7-21
****The manufacturing industry has undergone significant transformations over the last few decades, with technological advancements leading the way. One such advancement that stands out is the evolution of industrial tube making machinery. This machinery embodies the core of modern manufacturing processes, providing efficiency, precision, and sustainability in producing tubes that are essential across various industries.
Industrial tube making machinery encompasses a wide array of equipment and techniques used to produce tubes of different materials, including metals, plastics, and composites. The applications of these tubes are vast, ranging from construction and automotive industries to aerospace and medical sectors. As such, the demand for efficient and high-quality tube production is continuously on the rise, and this need has driven constant innovation within the industry.
At the heart of industrial tube making is the need for efficiency. Modern machinery is designed to streamline processes that were once labor-intensive and time-consuming. With the integration of automation and computer numerical control (CNC) systems, manufacturers can produce tubes with remarkable speed and precision. Automated systems reduce human error and enhance production rates, allowing facilities to meet the increasing demands of their customers.
Various processes are involved in tube making, including extrusion, drawing, and welding. Each method requires specialized machinery, and advancements have led to the development of machines that can handle multiple processes seamlessly. For instance, multi-functional tube making machines can perform tasks like cutting, bending, and welding, all in one setup. This not only saves time but also minimizes the need for manual intervention, further enhancing productivity and reducing operational costs.
One of the significant advancements in industrial tube making machinery is the introduction of more energy-efficient models. As industries increasingly face pressure to adopt sustainable practices, manufacturers are responding by developing machines that consume less energy while maintaining high output levels. Energy-efficient machinery not only lowers production costs but also reduces the carbon footprint of manufacturing operations, making it a win-win situation for businesses and the environment.
Moreover, the advent of smart technology in industrial tube making has redefined how manufacturers operate. Internet of Things (IoT) capabilities allow machines to communicate with each other and with operators, providing real-time data and analytics that enhance decision-making processes. Predictive maintenance, enabled by smart technology, helps identify potential issues before they cause significant downtime, thereby optimizing production schedules and reducing maintenance costs.
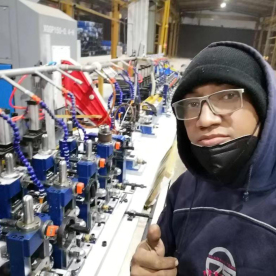
Exploring the Advances in Industrial Tube Making Machinery: Revolutionizing Manufacturing Processes for a Sustainable Future
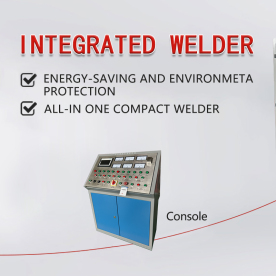
Exploring the Advances in Industrial Tube Making Machinery: Revolutionizing Manufacturing Processes for a Sustainable Future
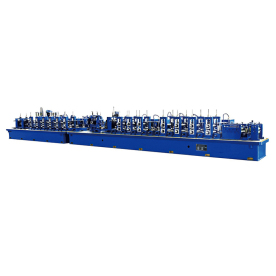
Exploring the Advances in Industrial Tube Making Machinery: Revolutionizing Manufacturing Processes for a Sustainable Future
In conclusion, industrial tube making machinery plays a vital role in shaping the future of manufacturing. Its capacity to deliver efficiency, precision, and adaptability directly impacts various sectors’ capabilities. As technological advancements continue to unfold, manufacturers that embrace these changes will not only enhance their operational effectiveness but also contribute to a more sustainable industrial landscape. With ongoing innovations, the future of tube production looks promising, paving the way for safer, more efficient, and environmentally friendly manufacturing processes.