[Pipe mill production line with welding and cutting functions]Exploring the Innovations and Efficiencies of Pipe Mill Production Lines Featuring Advanced Welding and Cutting Functions
News 2024-7-20
****In the fast-evolving world of manufacturing, pipe mill production lines have become integral to various industries, including construction, automotive, and energy. These production lines are increasingly characterized by their advanced technological capabilities, particularly in welding and cutting functions. As companies strive to improve efficiency, maintain high-quality standards, and meet the demands of a competitive market, the innovations in pipe mill production lines are noteworthy. This article delves into the various aspects of pipe mill production lines equipped with cutting-edge welding and cutting capabilities, exploring their significance, operational efficiencies, and future trends.
The Importance of Pipe Mill Production Lines
Pipe mill production lines represent a critical component in the supply chain of numerous industries. They help produce a wide range of pipes, such as welded pipes, seamless pipes, and other types designed for specific applications. With the global demand for piping solutions continuing to rise—driven by urbanization, infrastructure development, and the increasing need for energy—efficient production lines are essential. They must not only ensure quality but also deliver cost-effective solutions.
Integration of Welding Features
Welding is a pivotal function in the manufacturing of pipes. Traditional welding methods have been transformed by the advent of advanced technologies such as laser welding, high-frequency induction welding (HFIW), and submerged arc welding (SAW). Each of these methods has distinct advantages, allowing manufacturers to optimize their production processes based on the type of pipe being produced.
1. **Laser Welding**: This method provides high precision and minimal heat distortion, making it suitable for thin-walled piping. Its speed and precision enhance the overall productivity of the pipe mill.
2. **High-Frequency Induction Welding (HFIW)**: HFIW is widely used in the production of large diameter pipes. It allows for fast welding speeds while ensuring excellent joint strength.
3. **Submerged Arc Welding (SAW)**: Often used for thick-walled pipes, SAW enhances the quality of welds while reducing the likelihood of defects thanks to its controlled and stable process.
The integration of these welding technologies into pipe mill production lines significantly enhances their efficiency, ultimately meeting industry standards and customer expectations.
Advanced Cutting Functions
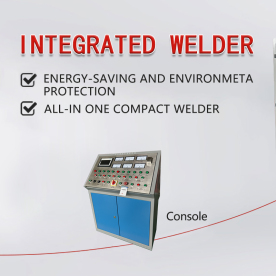
Exploring the Innovations and Efficiencies of Pipe Mill Production Lines Featuring Advanced Welding and Cutting Functions
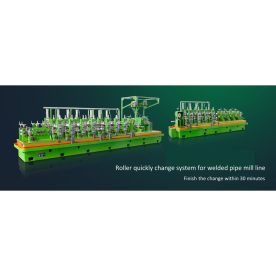
Exploring the Innovations and Efficiencies of Pipe Mill Production Lines Featuring Advanced Welding and Cutting Functions
1. **CNC Cutting Machines**: These machines utilize computer numerical control (CNC) to provide precise cuts, eliminating human error and ensuring uniformity throughout the production process.
2. **Plasma Cutting**: This technique allows for clean cuts in thick materials and can be automated for high-speed production. It is particularly useful in producing pipes that require unique dimensions.
3. **Waterjet Cutting**: This method uses high-pressure water mixed with abrasives to cut through materials without altering their properties due to heat. It is particularly beneficial for delicate materials that cannot withstand traditional cutting methods.
Operational Efficiencies
The combination of advanced welding and cutting features in pipe mill production lines results in significant operational efficiencies. These systems allow for real-time monitoring and adjustments during the manufacturing process, leading to waste reduction, improved labor allocation, and faster turnaround times. Automation is a key factor here; by minimizing human intervention, manufacturers can streamline their operations while maintaining high standards of safety and productivity.
The effective use of technology also enables manufacturers to gather data on production processes, providing insights for continuous improvement. With predictive maintenance, operators can address potential issues before they result in costly downtime, ensuring the reliability of the production line.
Future Trends

Exploring the Innovations and Efficiencies of Pipe Mill Production Lines Featuring Advanced Welding and Cutting Functions
In conclusion, pipe mill production lines equipped with advanced welding and cutting functions play a pivotal role in the manufacturing sector. By leveraging new technologies, manufacturers can improve efficiency, maintain high-quality standards, and meet the ever-growing demand for piping solutions in a range of applications. The future of this industry is bright, with ongoing innovations poised to redefine how pipes are produced and utilized globally.