[Pipe mill production line]Understanding the Pipe Mill Production Line: A Comprehensive Overview of Processes, Technologies, and Benefits in Modern Manufacturing
News 2024-7-20
****In the realm of manufacturing, efficiency, quality, and precision are paramount. One sector that exemplifies these attributes is the pipe manufacturing industry. The Pipe Mill Production Line is a sophisticated, meticulously designed system that automates the creation of pipes used in various applications, from construction to manufacturing and beyond. As technology advances, so too does the pipe mill production line, evolving to meet the demands of an ever-changing marketplace. In this article, we will delve into the intricacies of the pipe mill production line, its core components, manufacturing processes, and the substantial benefits it brings to modern manufacturing.
What is a Pipe Mill Production Line?
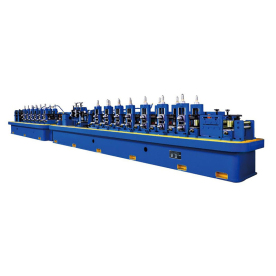
Understanding the Pipe Mill Production Line: A Comprehensive Overview of Processes, Technologies, and Benefits in Modern Manufacturing
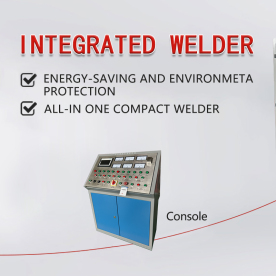
Understanding the Pipe Mill Production Line: A Comprehensive Overview of Processes, Technologies, and Benefits in Modern Manufacturing
Key Components of the Pipe Mill Production Line
1. **Uncoiler**: The journey begins with the uncoiler, which feeds the raw steel coil into the production line. The uncoiling process is critical as it sets the foundation for the steel to be processed into pipe form.
2. **Forming Station**: Once the coil is uncoiled, the steel is passed through a series of rollers that gradually shape it into the desired pipe profile. This can include various cross-section shapes, depending on the end-use requirements.

Understanding the Pipe Mill Production Line: A Comprehensive Overview of Processes, Technologies, and Benefits in Modern Manufacturing
4. **Sizing Mill**: After welding, the pipe enters the sizing mill, where it is passed through a series of rollers to achieve the desired diameter and wall thickness. This stage is vital in ensuring that the pipe meets precise specifications.
5. **Cut-off Machine**: Once the pipe reaches its required length, it is fed into a cut-off machine, where it is severed into individual pieces. Precision in this step is essential to ensure that all cut pipes meet the production specifications.
6. **Finishing Line**: The final stage of the production line involves a finishing line that may include processes such as surface treatment, inspection, and coating. The finishing stage ensures that the pipes are ready for delivery and meet any additional customer specifications.
Benefits of a Pipe Mill Production Line
The implementation of a pipe mill production line can yield numerous benefits to manufacturers, ensuring they remain competitive in their respective markets:
1. **Increased Production Efficiency**: By automating and streamlining the pipe manufacturing process, a pipe mill production line significantly reduces the time taken to produce high-quality pipes. This efficiency translates into higher output rates and improved profitability.
2. **Consistent Quality Control**: The integration of advanced technologies and machinery in the production line allows for precise control over various parameters. This consistency in quality ensures that every pipe produced meets industry standards and customer expectations.
3. **Cost Reduction**: With optimized processes, manufacturers can reduce labor costs and minimize scrap material, leading to overall cost savings. A more efficient production line can also reduce energy consumption.
4. **Versatility**: Modern pipe mill production lines can be designed to produce a wide variety of pipe sizes and specifications. This adaptability allows manufacturers to cater to diverse customer needs, from small-scale projects to large industrial applications.
5. **Enhanced Safety**: Automation reduces the risk of human error and enhances workplace safety. With machines handling most of the heavy lifting and repetitive tasks, the likelihood of workplace accidents decreases significantly.
Conclusion
The pipe mill production line stands as a testament to the innovation and sophistication of modern manufacturing. With its advanced processes and technologies, it not only streamlines the production of high-quality pipes but also provides manufacturers with a competitive edge in an evolving market. As industries continue to grow and diversify, the importance of efficient and reliable manufacturing processes—such as those offered by a pipe mill production line—will only increase, solidifying its role in the future of manufacturing.
This comprehensive overview of the pipe mill production line underscores its significance, emphasizing the necessity for manufacturers to embrace such technologies for sustainable growth and success in the industry.