[High-efficiency pipe mill production line]Revolutionizing Manufacturing: Understanding the High-Efficiency Pipe Mill Production Line for Enhanced Productivity and Quality
News 2024-7-20
In today’s ever-competitive manufacturing landscape, efficiency and quality are paramount, especially in the pipeline industry. With increasing global demand for steel pipes in various sectors, including construction, oil and gas, water supply, and sewage, the challenge of producing high-volume, high-quality pipes at a lower cost has never been more critical. This is where the concept of a High-Efficiency Pipe Mill Production Line comes into play, transforming traditional manufacturing practices and setting new standards in the industry.
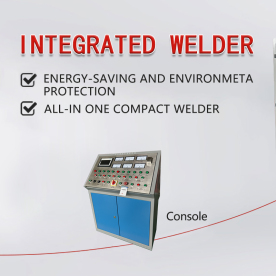
Revolutionizing Manufacturing: Understanding the High-Efficiency Pipe Mill Production Line for Enhanced Productivity and Quality
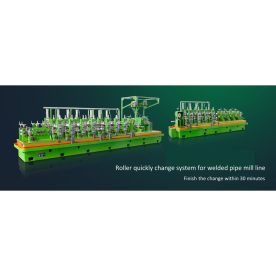
Revolutionizing Manufacturing: Understanding the High-Efficiency Pipe Mill Production Line for Enhanced Productivity and Quality
Once the steel is shaped into a pipe, the next critical stage is welding. Conventional welding techniques can be time-consuming and prone to fluctuations in quality. However, in a High-Efficiency Pipe Mill, various modern welding methods, such as high-frequency induction welding or laser welding, facilitate a quicker and more streamlined process. These techniques not only improve the speed of production but also enhance the structural integrity of the pipes. Automated welding systems equipped with precise sensors ensure that every weld is of uniform quality, further ensuring that the final product meets stringent industry standards.
After welding, pipes are subjected to various finishing processes for optimal surface quality and performance. This includes processes such as deburring, polishing, and coating – all of which are important to enhance the lifespan of the pipes and protect them from corrosion, particularly in industries like oil and gas where environmental factors can be particularly harsh. High-efficiency production lines utilize automated systems that make these finishing processes faster and more consistent.

Revolutionizing Manufacturing: Understanding the High-Efficiency Pipe Mill Production Line for Enhanced Productivity and Quality
Moreover, energy efficiency is a key consideration in modern manufacturing. High-Efficiency Pipe Mills are designed with energy-saving technologies that reduce power consumption, lowering the overall carbon footprint of the production process. This commitment to sustainability is not only essential for environmental reasons but also makes good economic sense in today's market where energy costs continue to rise.
The integration of data analytics and IoT (Internet of Things) technology further enhances the efficacy of the High-Efficiency Pipe Mill Production Line. By leveraging real-time data monitoring, manufacturers can identify bottlenecks and inefficiencies in the production process, allowing for continuous improvement. Predictive maintenance tools help to prevent unplanned downtime, ensuring that production schedules are met without costly interruptions.
In conclusion, the High-Efficiency Pipe Mill Production Line represents a transformative step forward in the production of steel pipes. By combining advanced technology with efficient processes, manufacturers can produce high-quality pipes at unprecedented rates while also being mindful of cost and environmental impact. As industries continue to evolve and demand increases, investing in high-efficiency production lines will be essential for companies looking to maintain a competitive edge in the global market. The future of pipe manufacturing is here, and it is efficient, sustainable, and poised for success.