[Pipe mill production line with quality control measures]Maximizing Efficiency and Quality Control Measures in a Pipe Mill Production Line
News 2024-7-5
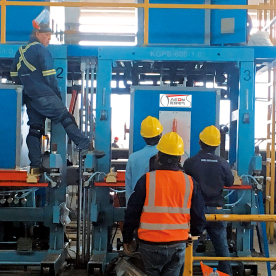
Maximizing Efficiency and Quality Control Measures in a Pipe Mill Production Line
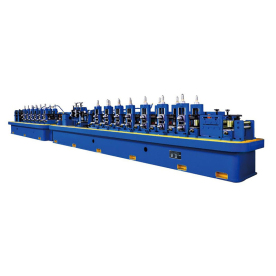
Maximizing Efficiency and Quality Control Measures in a Pipe Mill Production Line
A pipe mill production line typically consists of several key components, including a decoiler, a coil joining machine, a forming section, a welding station, a sizing section, a cooling zone, and a cut-off machine. Each of these components plays a vital role in shaping and welding the raw materials into the desired pipe shape and size. To maximize efficiency and maintain quality control during the production process, manufacturers implement a range of measures at each stage of the pipe mill production line.
One of the key quality control measures in a pipe mill production line is the use of advanced monitoring and inspection systems. These systems are equipped with sensors and cameras that can detect any defects or irregularities in the material, ensuring that only high-quality pipes are produced. In addition, manufacturers often employ automated feedback mechanisms that can make real-time adjustments to the production process to correct any issues that may arise.
Another important aspect of quality control in a pipe mill production line is the implementation of strict testing protocols. Before the finished pipes are released for sale, they undergo rigorous testing procedures to ensure that they meet industry standards for strength, durability, and dimensional accuracy. These tests may include hydrostatic testing, ultrasonic testing, and electromagnetic inspection, among others. By conducting thorough testing, manufacturers can identify any potential defects in the pipes and take corrective action before they are shipped to customers.
In addition to monitoring and testing, manufacturers also prioritize preventive maintenance in their pipe mill production lines. Regular inspections and maintenance checks are conducted on all machinery and equipment to ensure that they are operating at peak efficiency. By addressing any potential issues proactively, manufacturers can minimize downtime and prevent costly repairs, ultimately improving the overall productivity of the production line.
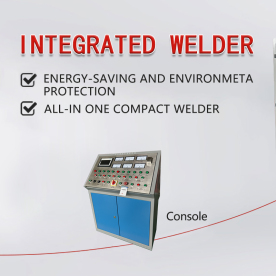
Maximizing Efficiency and Quality Control Measures in a Pipe Mill Production Line
In conclusion, maximizing efficiency and quality control measures in a pipe mill production line is crucial for producing high-quality pipes that meet the demands of various industries. By implementing advanced monitoring and inspection systems, conducting rigorous testing procedures, prioritizing preventive maintenance, and investing in employee training, manufacturers can ensure that their production lines operate at peak efficiency while consistently delivering top-notch pipes to their customers. With these measures in place, manufacturers can maintain a competitive edge in the highly competitive steel industry and continue to meet the ever-evolving needs of their clients.