[High frequency welder for plastic]Revolutionizing the Plastic Industry: High Frequency Welder for Plastic
News 2024-6-15
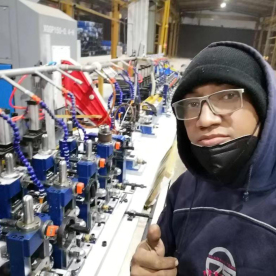
Revolutionizing the Plastic Industry: High Frequency Welder for Plastic
High frequency welders are particularly popular in industries such as packaging, automotive, and medical devices, where the durability and quality of welded plastics are of the utmost importance. These machines are capable of welding a wide range of plastics, including PVC, PET, and PE, making them versatile tools for manufacturers.
One of the key benefits of using a high frequency welder for plastic is the speed at which it can produce high-quality welds. Traditional welding methods can be time-consuming and require precise control of temperature and pressure, whereas high frequency welding is a much faster and more efficient process. This not only improves productivity but also reduces the risk of defects in the welded components.
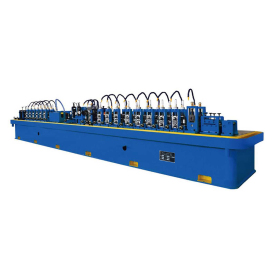
Revolutionizing the Plastic Industry: High Frequency Welder for Plastic
Another advantage of high frequency welders for plastic is the strength and integrity of the welds they produce. The electromagnetic waves used in the welding process create a strong bond between the plastic components, resulting in welds that are resistant to tearing, peeling, and other forms of mechanical stress. This makes high frequency welding an ideal choice for applications where durability is crucial.
In addition to the durability of the welds, high frequency welders also offer a high level of precision in the welding process. Because the heat is generated within the material itself, there is minimal risk of damage to the surrounding area, resulting in clean and uniform welds. This precision is essential for industries such as medical devices, where the integrity of the welded components is critical for the safety and efficacy of the final product.
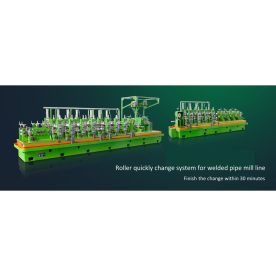