[High frequency welder]Revolutionizing the Industry with High Frequency Welder Technology
News 2024-6-10
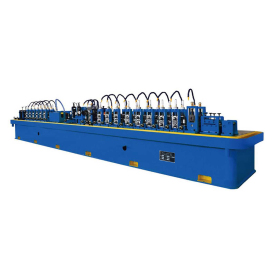
Revolutionizing the Industry with High Frequency Welder Technology
High frequency welding technology has been around for decades, but recent advancements in machinery and software have made it more versatile and reliable than ever before. With the ability to weld a wide range of materials, including plastics, synthetic fabrics, and even metal, high frequency welders have become an essential tool for a variety of industries.
One of the main benefits of using a high frequency welder is its speed and efficiency. By using electromagnetic waves to heat and bond materials together, the process is much faster than traditional welding methods. This not only saves time and labor costs but also increases production capacity, allowing manufacturers to meet tight deadlines and fulfill large orders with ease.
Another advantage of high frequency welding technology is its precision and consistency. The electromagnetic waves create a consistent and uniform heat source, ensuring that each weld is strong and reliable. This level of accuracy is especially important in industries like automotive manufacturing and medical equipment production, where even the smallest defect can have serious consequences.
In addition to speed and precision, high frequency welders are also environmentally friendly. Unlike traditional welding methods that use gas or chemicals, high frequency welding only requires electricity to generate the electromagnetic waves. This not only reduces the carbon footprint of manufacturing processes but also eliminates the need for hazardous materials, making it safer for workers and the environment.
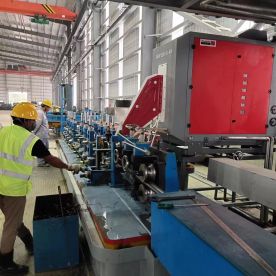
Revolutionizing the Industry with High Frequency Welder Technology

Revolutionizing the Industry with High Frequency Welder Technology
As high frequency welding technology continues to evolve, its applications are expanding into new industries and markets. From medical devices to inflatable products, the versatility and reliability of high frequency welders make them an essential tool for manufacturers around the world. With their speed, precision, and environmental benefits, high frequency welders are truly revolutionizing the industry and shaping the future of manufacturing.