[High frequency welder for plastic]Revolutionizing Plastic Welding: The Power of High Frequency Welder for Plastic
News 2024-5-30
Plastic welding has been a common industrial process for joining thermoplastic materials together. It is widely used in various industries such as automotive, packaging, medical devices, and electronics. Traditionally, plastic welding was done through methods like hot plate welding, ultrasonic welding, and solvent welding. However, with the advancements in technology, a new player has emerged in the plastic welding scene – the high frequency welder.
High frequency welding, also known as radio frequency welding, uses electromagnetic energy to create heat and bond thermoplastic materials together. This process offers several advantages over traditional welding methods, making it a preferred choice for many manufacturers.
One of the key benefits of using a high frequency welder for plastic is its speed and efficiency. Unlike hot plate welding, which requires heated platens to melt the plastic, high frequency welding can rapidly heat the material within seconds. This results in faster cycle times and increased productivity for manufacturers.
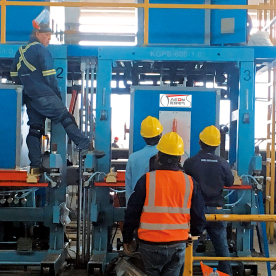
Revolutionizing Plastic Welding: The Power of High Frequency Welder for Plastic
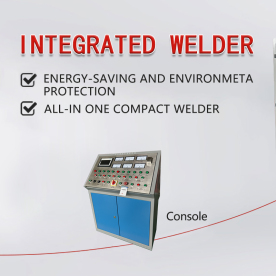
Revolutionizing Plastic Welding: The Power of High Frequency Welder for Plastic
Another advantage of high frequency welding is its versatility. It can be used to weld a wide range of thermoplastic materials, including PVC, PET, PU, and TPU. This flexibility allows manufacturers to work with different types of plastics without the need for multiple welding machines.

Revolutionizing Plastic Welding: The Power of High Frequency Welder for Plastic
In conclusion, high frequency welders have revolutionized the plastic welding industry with their speed, efficiency, durability, versatility, and eco-friendliness. As manufacturers continue to seek innovative and sustainable solutions, high frequency welding is set to become the go-to method for joining plastic materials. Its superior performance and cost-effectiveness make it an attractive option for various industries looking to streamline their production processes.