[Roller for tube mill]Enhancing Efficiency and Quality with the Right Roller for Tube Mill
News 2024-5-25
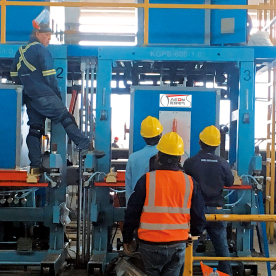
Enhancing Efficiency and Quality with the Right Roller for Tube Mill
Rollers come in different sizes, materials, and designs, each serving a specific purpose in the tube mill operation. The key to maximizing efficiency and quality lies in selecting the right roller for the job.
One of the most important factors to consider when choosing a roller for your tube mill is the material. The material of the roller will determine its durability, resistance to wear and tear, and overall performance. Common materials used for rollers include tool steel, stainless steel, and carbide. Each material has its advantages and disadvantages, so it's essential to consider your specific production needs when selecting the material for your rollers.
Another critical factor to consider when choosing a roller for your tube mill is the design. The design of the roller will impact the speed, precision, and quality of the tube mill operation. Some common roller designs include straight rollers, grooved rollers, and spiral rollers. The design of the roller should be chosen based on the specific requirements of your tube mill operation.
In addition to material and design, the size of the roller is also an essential factor to consider. The size of the roller will determine the diameter and thickness of the tubes produced by the tube mill. Choosing the right size roller is crucial for achieving the desired dimensions and tolerances in your tube mill operation.
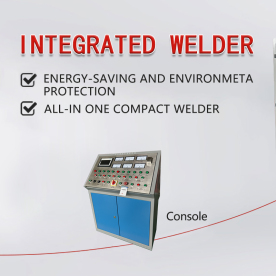
Enhancing Efficiency and Quality with the Right Roller for Tube Mill
When it comes to selecting the right roller for your tube mill, it is essential to consult with experts in the field. Experienced engineers and manufacturers can provide valuable insights and recommendations based on your specific production requirements. By working with professionals, you can ensure that you are choosing the right roller for your tube mill to enhance efficiency and quality.
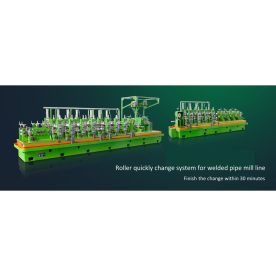