[Roller for tube mill]Improving Tube Mill Efficiency with High-Quality Rollers
News 2024-5-23
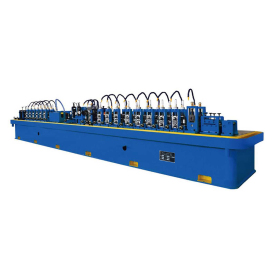
Improving Tube Mill Efficiency with High-Quality Rollers
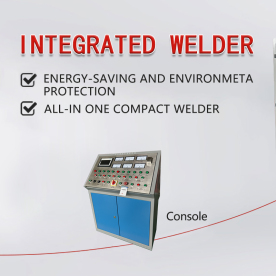
Improving Tube Mill Efficiency with High-Quality Rollers
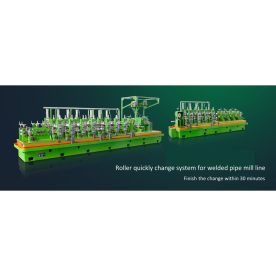
Improving Tube Mill Efficiency with High-Quality Rollers
Investing in high-quality rollers for a tube mill can significantly improve efficiency and productivity in the manufacturing process. Here are some key benefits of using high-quality rollers:
1. Improved Product Quality: High-quality rollers ensure precise shaping and guiding of the metal, resulting in tubes with accurate dimensions and consistent wall thickness. This leads to improved product quality and reduced scrap rates, ultimately enhancing customer satisfaction.
2. Increased Production Speed: High-quality rollers can withstand higher rolling speeds and pressures, allowing for faster production cycles. This increased production speed results in higher output and overall efficiency in the manufacturing process.
3. Reduced Downtime: Inferior quality rollers are prone to wear and damage, leading to frequent breakdowns and maintenance issues. Investing in high-quality rollers with durable materials and advanced coatings can help reduce downtime and maintenance costs, ensuring continuous operation of the tube mill.
4. Longevity and Cost Savings: High-quality rollers are designed to withstand the rigors of the tube mill environment, resulting in longer service life and reduced replacement costs. While the initial investment in high-quality rollers may be higher, the long-term cost savings and improved performance make it a worthwhile investment for tube mill operators.
When selecting rollers for a tube mill, it is essential to consider factors such as material quality, surface hardness, and precision machining. High-quality rollers are typically made from hardened tool steel or advanced alloys that offer superior durability and wear resistance. Surface treatments such as chrome plating or carbide coating can further enhance the performance and longevity of the rollers.
In conclusion, rollers are a critical component of a tube mill, and investing in high-quality rollers can have a significant impact on efficiency, productivity, and product quality. Tube mill operators should prioritize quality when selecting rollers to ensure optimal performance and long-term cost savings. By choosing high-quality rollers, manufacturers can improve their competitiveness in the market and meet the demands of their customers with precision-engineered tubes.