[High frequency welder for metal]Revolutionizing Metal Fabrication with High Frequency Welder Technology
News 2024-5-12
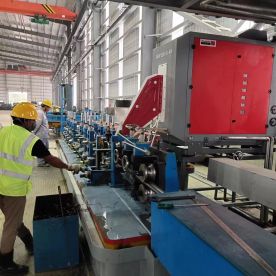
Revolutionizing Metal Fabrication with High Frequency Welder Technology
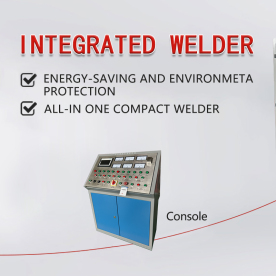
Revolutionizing Metal Fabrication with High Frequency Welder Technology

Revolutionizing Metal Fabrication with High Frequency Welder Technology
Another advantage of high frequency welders is their versatility. These machines can be used to weld a wide range of metals, including steel, aluminum, and copper. They can also be used to weld metal of varying thicknesses, making them ideal for a variety of applications. Whether you're working on a delicate sheet metal project or a heavy-duty structural application, a high frequency welder can get the job done with ease.
One of the key features of high frequency welders is their energy efficiency. Because the heat is generated directly in the metal, there is minimal heat loss during the welding process. This not only saves energy but also reduces the risk of warping or other distortions in the metal being welded. Additionally, high frequency welders produce minimal smoke, fumes, and other pollutants, making them a more environmentally friendly option for metal fabrication.
Overall, high frequency welders have truly revolutionized the metal fabrication industry. With their speed, precision, versatility, and energy efficiency, these machines offer a level of performance that traditional welding techniques simply can't match. Whether you're a small job shop or a large-scale manufacturer, investing in a high frequency welder can help take your metal fabrication capabilities to the next level. So why wait? Upgrade to high frequency welding technology today and experience the difference for yourself.