[IF pipe seam annealing machine ]Revolutionizing Pipeline Ma
News 2024-5-3
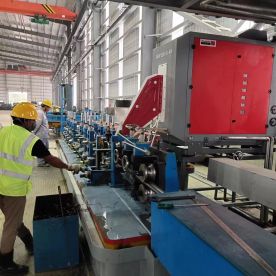
Revolutionizing Pipeline Manufacturing with the IF Pipe Seam Annealing Machine
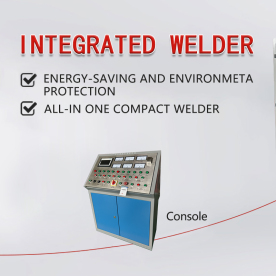
Revolutionizing Pipeline Manufacturing with the IF Pipe Seam Annealing Machine
To address this challenge, many pipeline manufacturers are turning to innovative technologies such as the IF Pipe Seam Annealing Machine. This cutting-edge device is designed to heat-treat the weld seam of pipes, ensuring that they have a consistent and uniform structure that is resistant to cracking and corrosion. By utilizing this advanced technology, pipeline manufacturers can improve the quality and reliability of their products, ultimately leading to safer and more durable pipelines.
So, what exactly is the IF Pipe Seam Annealing Machine, and how does it work? This state-of-the-art machine uses induction heating to heat-treat the weld seam of pipes. Induction heating is a process where an electrical current is passed through a conductive material, generating heat through electromagnetic induction. This method allows for precise and localized heating, ensuring that only the weld seam is heated and not the entire pipe.
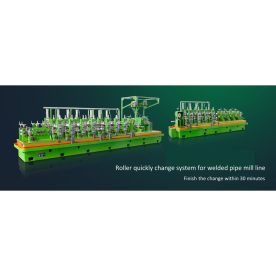
Revolutionizing Pipeline Manufacturing with the IF Pipe Seam Annealing Machine
Another advantage of the IF Pipe Seam Annealing Machine is its versatility and adaptability to different pipe sizes and materials. This machine can be easily adjusted to accommodate pipes of various diameters and wall thicknesses, making it suitable for a wide range of pipeline manufacturing applications. Furthermore, the precise control offered by this machine allows for customized heating profiles to be created, ensuring that each weld seam is treated according to specific requirements.
In addition to its technical capabilities, the IF Pipe Seam Annealing Machine also offers practical benefits for pipeline manufacturers. The compact and portable design of this machine makes it easy to transport and set up in a factory or on-site, saving valuable time and resources. Additionally, the user-friendly interface and automated controls of the machine make it simple to operate, reducing the need for specialized training or skilled labor.
Overall, the IF Pipe Seam Annealing Machine represents a significant advancement in pipeline manufacturing technology. By harnessing the power of induction heating, this machine offers a superior solution for heat-treating weld seams, ensuring the quality and durability of pipelines. As the demand for high-quality pipelines continues to grow, the IF Pipe Seam Annealing Machine is poised to revolutionize the industry and set new standards for pipeline manufacturing.