[Replacement Moulds for Tube Mills]Increasing Efficiency wit
News 2024-4-29
When it comes to maximizing efficiency and productivity in tube mill operations, having the right tools and equipment is key. One crucial component in tube mill production is the mould, which plays a critical role in shaping and forming tubes. Over time, moulds can wear down and become less effective, leading to decreased quality and productivity. This is where replacement moulds for tube mills come into play.
Replacement moulds for tube mills are specially designed to fit seamlessly into existing machinery, providing a quick and effective solution to worn-out or damaged moulds. By investing in high-quality replacement moulds, manufacturers can extend the lifespan of their equipment and ensure consistent output quality. In this article, we will explore the benefits of using replacement moulds for tube mills and why they are a worthwhile investment for tube mill operators.
One of the primary advantages of using replacement moulds for tube mills is the ability to maintain production consistency. As moulds age and wear down, they can lead to variations in tube dimensions and quality. This can result in rejected products, increased downtime for adjustments, and decreased overall productivity. By regularly replacing worn-out moulds with new ones, manufacturers can ensure that their products meet the required specifications and maintain a high level of quality.
In addition to maintaining consistent production quality, replacement moulds for tube mills can also help improve overall efficiency. Worn-out moulds can cause disruptions in the production process, leading to delays and increased operational costs. By replacing moulds on a regular basis, manufacturers can minimize downtime and keep their production lines running smoothly. This not only improves efficiency but also helps reduce overall maintenance costs associated with equipment repairs.
Furthermore, using replacement moulds for tube mills can also help extend the lifespan of other critical machine components. As moulds wear down, they can put increased strain on other parts of the machinery, leading to premature wear and potential breakdowns. By proactively replacing worn-out moulds, manufacturers can protect their equipment and avoid costly repairs or replacements down the line.
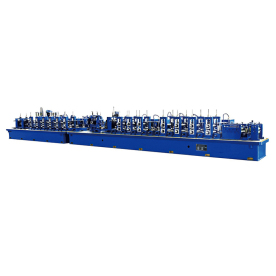
Increasing Efficiency with Replacement Moulds for Tube Mills
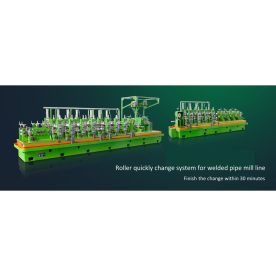
Increasing Efficiency with Replacement Moulds for Tube Mills
