[High frequency welder for plastic]Revolutionizing Plastic W
News 2024-4-23
High-frequency welders have become increasingly popular in the plastic manufacturing industry due to their efficiency and effectiveness in joining plastic materials. These advanced welding machines use high-frequency electromagnetic waves to generate heat and create strong bonds between plastic components.
One of the main advantages of high-frequency welders is their ability to produce consistent and precise welds, ensuring the quality and integrity of the finished product. Unlike traditional welding methods that rely on hot air or contact heat, high-frequency welding does not require direct contact with the material, reducing the risk of damage or distortion to the plastic parts.
The high-frequency welding process is also much faster compared to traditional methods, allowing manufacturers to increase production output and meet tight deadlines. This is especially important in industries such as automotive, medical, and packaging, where speed and efficiency are essential for meeting customer demands.
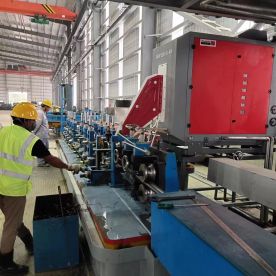
Revolutionizing Plastic Welding with High-Frequency Welders
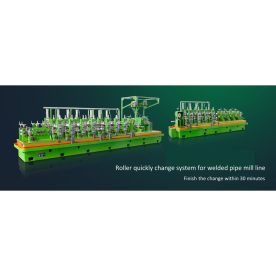
Revolutionizing Plastic Welding with High-Frequency Welders

Revolutionizing Plastic Welding with High-Frequency Welders
Overall, high-frequency welders are revolutionizing the plastic welding industry with their speed, precision, versatility, energy efficiency, and ease of use. As manufacturers continue to adopt these advanced machines, we can expect to see even greater advancements in plastic welding technology, driving innovation and growth in the industry for years to come.