[High frequency welder for plastic]insert website link
News 2025-4-17
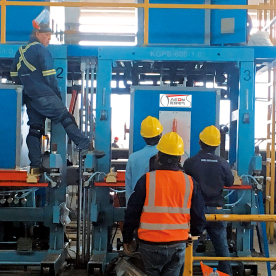
insert website link
In the realm of plastics processing, high frequency welder stands out as a critical machine that guarantees seamless welding with impeccable quality. If you're in the market for a high frequency welder for plastic, this guide will help you make an informed decision and ensure optimal operation.
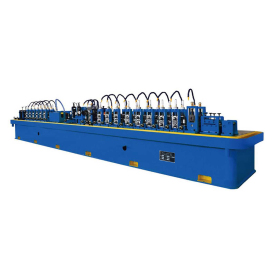
insert website link
A high frequency welder for plastic is a machine that uses high-frequency electromagnetic fields to generate heat for the purpose of welding plastic materials. This welding process is suitable for a wide range of plastic materials, including polyethylene, polypropylene, PVC, and more.
Why Use High Frequency Welding? ---------------
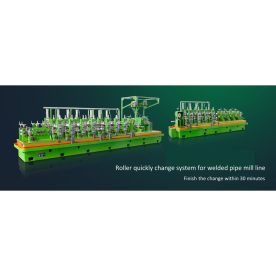
insert website link
Types of High Frequency Welders for Plastic -----------------------
When selecting a high frequency welder for plastic, you'll find several types tailored to different applications and material types. Here are some of the common types:
1. Tabletop High Frequency Welders: These are compact welders designed for small-scale production and lab use. They're easy to operate and offer good welding performance for a range of plastic materials. 2. Industrial High Frequency Welders: These are robust machines designed for high-volume production. They come with advanced features like automatic control systems and adjustable welding parameters to ensure consistent welding quality. 3. Custom High Frequency Welders: These are tailor-made welders designed to meet specific requirements like welding unusual material combinations or complex shapes. They offer flexibility and customization options to meet unique application needs.
How to Select the Right High Frequency Welder for Plastic? -------------------------------
When selecting a high frequency welder for plastic, consider the following factors:
1. Material Type: Different welders are suitable for different plastic materials. Make sure the welder you choose is compatible with your material of choice. 2. Production Requirements: Consider your production volume and the size of the parts you need to weld. This will help you choose the right size and capacity of the welder. 3. User-Friendliness: Look for welders that are easy to operate and maintain. This will ensure smooth operation and reduce downtime. 4. Cost: High frequency welders come in different price ranges. Make sure you choose a welder that fits your budget without compromising on performance and quality. 5. After-Sales Support: Look for manufacturers that offer good after-sales support like technical assistance, spare parts, and training. This will ensure you get the most out of your investment.
How to Operate a High Frequency Welder for Plastic? --------------------------
Operating a high frequency welder for plastic is relatively straightforward but still requires some attention to detail and safety measures. Here are some key steps to follow:
1. Set up the welder according to the manufacturer's instructions. Make sure the power supply is connected securely and the machine is properly grounded. 2. Prepare the plastic parts to be welded by cleaning them and removing any debris or contaminants. 3. Adjust the welding parameters according to your material and application requirements. This includes setting the right welding time, pressure, and temperature. 4. Place the plastic parts in the correct position on the welding table and secure them in place if necessary. 5. Start the welder and monitor the welding process closely to ensure proper bonding and no defects like incomplete welds or excessive heat damage. 6. After welding, allow the parts to cool down before handling them to avoid any damage or deformation due to residual stress or heat buildup. Follow any post-welding inspection procedures specified by the manufacturer to ensure proper quality control measures are implemented. Take regular maintenance checks on your equipment to ensure its longevity and performance efficiency over time." 7 Conclusion The high frequency welder for plastic is an essential tool in any plastics processing operation that requires seamless bonding of plastic materials with precision quality results achieved consistently without compromise over time usage Of this equipment offers efficient productivity at a reasonable cost with added advantages like low material waste and increased overall profitability As you make your decision on purchasing a high frequency welder ensure you understand its capabilities limitations operating procedures maintenance requirements as well as safety measures required for effective operation To maximize productivity quality outcomes while minimizing risks consider consulting with industry experts who can guide you through every step of selecting operating your high frequency welder for plastic successfully." 8 Resources For further information on high frequency welders visit our website at where we provide detailed specifications features videos tutorials on how to operate maintain your equipment as well as industry insights trends that can help you make informed decisions about your investment Contact us today at [insert contact details] for any questions