[High frequency welder]High Frequency Welder: The Heart of Efficient Metal Fabrication Processes
News 2025-4-2
In various industrial sectors, high frequency welding machines play a pivotal role in the efficient production of metal components. High frequency welders are used to join together pieces of metal with precision and speed, enhancing productivity and reducing defects in the final product. In this article, we will explore the importance of high frequency welders in metal fabrication processes and how they contribute to the overall efficiency of manufacturing operations.
What is a High Frequency Welder?
A high frequency welder is a specialized machine designed to use high-frequency electrical current to generate heat at a precise point for the purpose of welding metal parts. It operates by focusing a high-frequency electrical current on the joint to be welded, causing the metal molecules to collide and fuse together. This process offers several advantages over traditional welding methods, including faster welding speeds, reduced heat input, and improved joint quality.
How Does a High Frequency Welder Work?
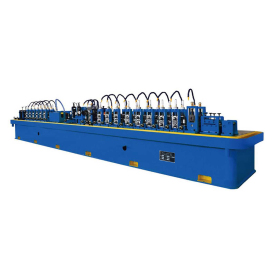
High Frequency Welder: The Heart of Efficient Metal Fabrication Processes
Advantages of High Frequency Welders
1. Speed: High frequency welders offer significantly faster welding speeds compared to traditional welding methods. This results in increased productivity and reduced manufacturing cycle times. 2. Quality: The precision of high frequency welding ensures consistent joint quality with minimal defects. This leads to a higher quality final product with fewer rejections and rework. 3. Cost-efficiency: Faster welding speeds and reduced defects result in cost savings for manufacturers. Additionally, high frequency welders require less operator intervention, further reducing labor costs. 4. Versatility: High frequency welders can be used to weld various types of metals, including steel, aluminum, copper, and their alloys. This versatility allows manufacturers to use the same equipment for multiple applications, enhancing their ability to adapt to changing market demands.
Applications of High Frequency Welders
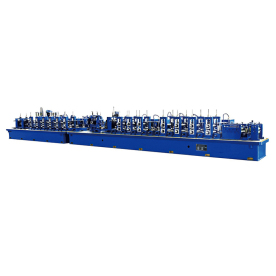
High Frequency Welder: The Heart of Efficient Metal Fabrication Processes
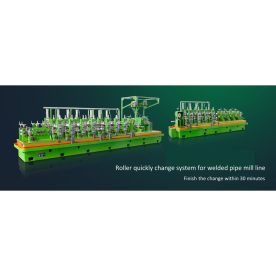
High Frequency Welder: The Heart of Efficient Metal Fabrication Processes
High frequency welders are essential for efficient metal fabrication processes in various industries. Their ability to offer fast, precise welding with minimal defects makes them a valuable tool for manufacturers seeking to enhance productivity and reduce costs. With continued advancements in technology, high frequency welders are becoming more versatile and capable of meeting the demands of a wide range of manufacturing applications.