[ERW tube mill]Understanding the Advantages and Applications of ERW Tube Mill Technology in Modern Manufacturing
News 2025-1-30
****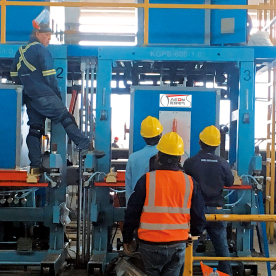
Understanding the Advantages and Applications of ERW Tube Mill Technology in Modern Manufacturing
What is an ERW Tube Mill?
The ERW tube mill is a specialized manufacturing unit that produces welded tubes and pipes by forming a flat strip or coil of metal into a cylindrical shape. The edges of the metal are then joined together by applying heat generated from electric resistance welding. The process is highly efficient and can create seamless and continuous lengths of tubing that meet high standards for strength and durability.
How Does an ERW Tube Mill Work?
The operation of an ERW tube mill begins with the feeding of metal strips into the machine. Typically made of various materials such as carbon steel, stainless steel, or aluminum, these strips are unrolled and directed through a series of rollers that gradually form them into a cylindrical shape. At this point, the edges are aligned precisely to ensure a strong bond once welded.
The core of an ERW tube mill is the welding unit, which uses electric current to generate heat at the edges of the metal strips. This heat causes the metal to reach a plastic state, allowing it to fuse without additional filler material. The controller ensures that the parameters such as temperature and pressure are optimal for a high-quality weld. After welding, the tube is cooled down, and further processes such as cutting, straightening, and inspection may follow.
Advantages of Using ERW Tube Mills
1. **Cost-Efficiency**: One of the significant benefits of ERW tube mills is their cost-effectiveness. The processes involved are less labor-intensive compared to traditional methods, which helps reduce production costs. Additionally, the ability to produce high-strength tubes from thin sheets of metal minimizes material wastage.
2. **High Production Speed**: ERW tube mills can operate at high speeds, allowing manufacturers to produce large volumes of tubular products in a shorter time. This is particularly advantageous for businesses that demand quick turnaround times to meet market needs.
3. **Versatility**: ERW tube mills can produce a wide variety of tube sizes and shapes, accommodating specific industry requirements. From small-diameter pipes used in plumbing to larger structures for energy and construction, the versatility of ERW technology allows for tailored solutions.
4. **Quality and Consistency**: The automated nature of the ERW tube mill process ensures uniformity and high quality across all products. Advanced control systems monitor the welding process in real time, significantly reducing the risk of defects and enhancing durability.
5. **Minimal Heat Affected Zone**: Unlike processes that rely on fusion welding, the heat-affected zone in ERW welding is minimal. This allows for high-quality welds that maintain the strength and integrity of the base material.
Applications of ERW Tube Mills
The influence of ERW tube mills stretches across numerous industries. Here are a few key sectors where its technology plays a vital role:
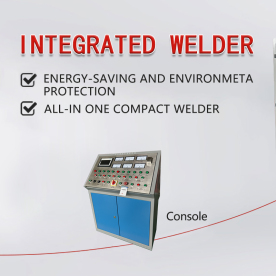
Understanding the Advantages and Applications of ERW Tube Mill Technology in Modern Manufacturing
2. **Oil and Gas**: In the oil and gas industry, ERW tubes are used for drilling, casing, and transporting liquids and gases. The high-pressure resistance of these tubes is crucial for ensuring safe and reliable operations.
3. **Automotive**: ERW tubes find applications in the automotive sector for components such as exhaust systems and chassis parts. The ability to produce tubes that meet precise specifications is vital for modern vehicle manufacturing.
4. **Furniture and Appliances**: The versatility of ERW tube mills extends to the production of furniture frames and appliance components. The aesthetic appeal combined with structural integrity makes ERW tubes a favored choice in design.

Understanding the Advantages and Applications of ERW Tube Mill Technology in Modern Manufacturing
The ERW tube mill represents a significant advancement in the manufacturing sector, delivering high-quality, cost-effective, and versatile solutions for various industries. Its operational principles revolving around electric resistance welding set it apart from traditional tube manufacturing techniques. As industries continue to evolve and demand more efficient products, the ERW tube mill will undoubtedly remain at the forefront of technological innovation, driving progress and ensuring robust solutions for the future.