[Advanced induction heating equipment technology]Exploring the Future of Manufacturing: The Role of Advanced Induction Heating Equipment Technology in Enhancing Efficiency and Productivity
News 2025-1-29
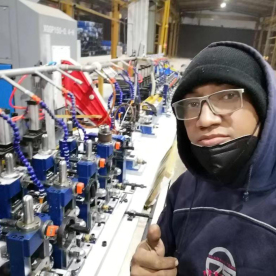
Exploring the Future of Manufacturing: The Role of Advanced Induction Heating Equipment Technology in Enhancing Efficiency and Productivity
The evolution of manufacturing has been significantly shaped by technological advancements, among which advanced induction heating equipment technology stands out as a game-changer. This technology, based on the principles of electromagnetic induction, has revolutionized how metals and other materials are heated in various industrial applications. As industries continue to seek innovative solutions to improve efficiency, reduce costs, and enhance product quality, advanced induction heating equipment has emerged as a vital tool in achieving these objectives.
Induction heating technology operates by generating heat within the workpiece through electromagnetic fields. This method contrasts sharply with traditional heating techniques, such as convection or conduction, which often result in heat loss and uneven temperature distribution. Advanced induction heating systems utilize sophisticated electronics and sensors to provide precise control over heating variables, such as temperature and time. As a result, manufacturers can achieve consistent, high-quality outcomes, which is particularly critical in processes like hardening, melting, forging, and brazing.
One of the primary advantages of advanced induction heating equipment is its energy efficiency. Traditional heating methods can consume substantial energy and lead to significant operational costs. In contrast, induction heating systems are known for their high energy efficiency, often achieving over 90% efficiency rates. This efficiency not only lowers energy bills but also minimizes the carbon footprint of manufacturing processes, aligning with the growing emphasis on sustainability.
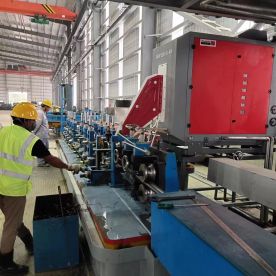
Exploring the Future of Manufacturing: The Role of Advanced Induction Heating Equipment Technology in Enhancing Efficiency and Productivity
The flexibility of advanced induction heating technology also plays a crucial role in its growing popularity. With the capability to accommodate various materials, including ferrous and non-ferrous metals, the equipment can be tailored to specific applications, making it a versatile solution for diverse industries—from automotive and aerospace to electronics and heavy machinery. Additionally, advancements in control systems enable operators to fine-tune the induction heating process to the specific needs of each part being machined.
Safety features integrated into advanced induction heating equipment further enhance its appeal. Traditional heating methods can pose several risks, including burns and exposure to harmful fumes. In contrast, induction heating systems generate very little residual heat in their surroundings, reducing the risk of accidents. Furthermore, with robust monitoring systems in place, operators can quickly identify and respond to potential malfunctions, ensuring a safer working environment.
The implementation of advanced induction heating technology is not only beneficial for manufacturers but also contributes positively to the broader supply chain. Improved quality and consistency reduce the frequency of defects and rework, which can disrupt production and inflate costs. By streamlining operations and enhancing product integrity, manufacturers can deliver goods more reliably, improving customer satisfaction and fostering long-term loyalty.
In recent years, the development of smart induction heating technology has taken center stage. These systems utilize artificial intelligence and IoT (Internet of Things) connectivity to monitor conditions in real-time, enabling predictive maintenance and further optimization of heating processes. By analyzing data collected from various sensors, manufacturers can anticipate equipment failures before they occur and adjust operations to avoid downtime, thus maintaining continuous production flow.
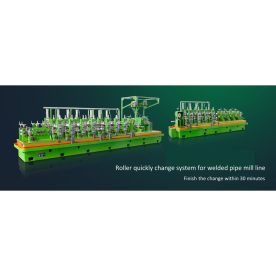
Exploring the Future of Manufacturing: The Role of Advanced Induction Heating Equipment Technology in Enhancing Efficiency and Productivity
In conclusion, advanced induction heating equipment technology is transforming the landscape of manufacturing by providing energy-efficient, precise, and safe heating solutions. Its versatility and ability to enhance productivity make it an indispensable tool for manufacturers aiming to thrive in an increasingly competitive marketplace. As innovation in this field continues to progress, the potential applications and advantages of induction heating promise to expand, further solidifying its role in shaping the future of manufacturing.