[High frequency welder machine]Exploring the Benefits and Applications of High Frequency Welder Machines in Modern Manufacturing Processes
News 2025-1-28
In the era of advanced manufacturing and automation, high frequency welder machines have emerged as a powerful tool in the fabrication industry. These state-of-the-art machines utilize electromagnetic technology to produce high-quality welds efficiently and effectively. Their application spans various sectors, including automotive, aerospace, electronics, and textiles, leading to a significant transformation in how products are manufactured and assembled. This article delves into the benefits and applications of high frequency welder machines, highlighting their importance in modern manufacturing.
**Understanding High Frequency Welding Technology**
High frequency welding, also known as radio frequency welding, employs electromagnetic waves to generate heat within the materials being joined. In this method, high-frequency radio waves (typically between 13.56 MHz and 27.12 MHz) pass through the thermoplastic materials, causing them to soften and bond together as they are subjected to pressure. This process allows for rapid and efficient welding, resulting in strong seams that can withstand various stress factors.
The technology is particularly advantageous for materials that are difficult to weld using conventional methods, such as certain plastics and composites. The ability to join materials without the need for additional adhesives or mechanical fasteners further enhances the appeal of high frequency welding.
**Advantages of High Frequency Welder Machines**
1. **Speed and Efficiency:** High frequency welders are known for their rapid operation. With the ability to weld materials quickly, manufacturers can increase production rates, reduce cycle times, and ultimately lower labor costs. This increased efficiency directly impacts the bottom line, making high frequency welders a prudent investment for many businesses.
2. **Consistency and Quality:** One of the most critical factors in manufacturing is product quality. High frequency welders deliver consistent welds with minimal variability, ensuring that each product meets quality standards. The precision of the welding process also reduces the likelihood of defects, leading to fewer reworks and increasing customer satisfaction.
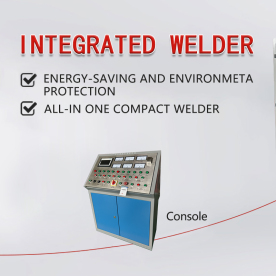
Exploring the Benefits and Applications of High Frequency Welder Machines in Modern Manufacturing Processes
4. **Cost-Effectiveness:** While the initial investment in high frequency welding equipment can be significant, the long-term cost savings achieved through increased productivity and reduced material waste are substantial. Furthermore, the energy-efficient nature of these machines means lower operational costs over time.
5. **No Need for Additional Materials:** Unlike conventional welding that may require fillers, adhesives, or other bonding agents, high frequency welding joins materials without the need for extra substances. This characteristic not only simplifies the manufacturing process but also results in cleaner, more environmentally friendly production methods.
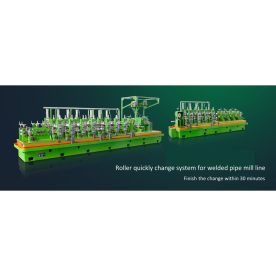
Exploring the Benefits and Applications of High Frequency Welder Machines in Modern Manufacturing Processes
High frequency welder machines find their application across numerous industries:

Exploring the Benefits and Applications of High Frequency Welder Machines in Modern Manufacturing Processes
- **Textile Industry:** The use of high frequency welding is prevalent in making banners, tarpaulins, and outdoor gear, where strong, waterproof seams are essential.
- **Medical Field:** High frequency welders play a crucial role in producing medical devices, such as IV bags and surgical drapes, where sterility and reliability are of utmost importance.
- **Packaging Industry:** They are employed in the production of flexible packaging solutions, including bags and pouches, which require strong seals to maintain product integrity.
- **Electronics:** In electronics manufacturing, high frequency welding is used to create hermetic seals for components requiring protection from the elements, enhancing durability and performance.
**Conclusion**
High frequency welder machines represent a significant advancement in welding technology, offering an array of benefits that enhance manufacturing efficiency, product quality, and versatility. As industries increasingly demand high-quality and consistent products, the adoption of high frequency welding techniques will likely continue to rise. By embracing this innovative technology, manufacturers can not only improve their production processes but also stay competitive in a rapidly evolving market landscape. The future of manufacturing looks bright with high frequency welder machines at the forefront.