[Durable Mould for Tube Mills]Exploring the Importance of Durable Mould for Tube Mills in Enhancing Production Efficiency and Product Quality
News 2025-1-28
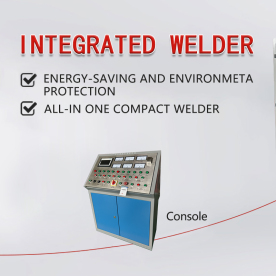
Exploring the Importance of Durable Mould for Tube Mills in Enhancing Production Efficiency and Product Quality
Durable moulds are designed to withstand the harsh environments of tube mills, where factors such as high temperatures, considerable stress, and chemical exposure are prevalent. Choosing the right materials and manufacturing processes for moulds is essential in achieving the desired life expectancy and performance. Many manufacturers opt for high-grade steel alloys, which offer excellent wear resistance and strength, ensuring that the moulds can endure the rigors of high-volume production.
One of the foremost advantages of using durable moulds in tube mills is the improvement in product quality. Moulds that maintain their shape and structural integrity over time lead to greater consistency in the tubes produced. This is particularly important in industries where precision is paramount. For instance, in the automotive sector, where tubes are used for exhaust systems and structural components, even minor deviations can lead to significant performance issues and safety hazards. Durable moulds help minimize these risks by providing the stability needed for precise tube dimensions.
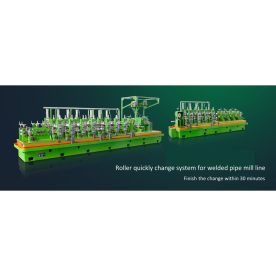
Exploring the Importance of Durable Mould for Tube Mills in Enhancing Production Efficiency and Product Quality
The manufacturing of durable moulds for tube mills also embraces technological innovations. Advances in casting techniques, such as precision casting and the use of computer-aided design (CAD), have revolutionized the way moulds are produced. These technologies enable manufacturers to create intricate designs that not only enhance the performance of the mould but also facilitate better cooling and heat management during the tube production process. This is particularly important in welded tube mills, where controlled cooling processes are essential to avoid warping and ensure strength.

Exploring the Importance of Durable Mould for Tube Mills in Enhancing Production Efficiency and Product Quality
Furthermore, the operational environment of tube mills necessitates the ongoing need for maintenance and lubrication. Regular inspections and proper upkeep of durable moulds can dramatically extend their service life. Manufacturers are increasingly adopting predictive maintenance strategies, utilizing sensors and data analytics to monitor the condition of moulds and plan maintenance schedules proactively. This approach minimizes unexpected failures and maximizes production uptime.
Finally, the importance of durable moulds extends beyond the individual manufacturing facility. As global supply chains become more interconnected, the demand for high-quality tubes has surged. Manufacturers that prioritize the use of durable moulds position themselves as reliable suppliers capable of meeting the stringent quality demands of various sectors. This not only enhances a company's reputation in the marketplace but also fosters customer loyalty and long-term business relationships.
In conclusion, the impact of durable moulds on tube mills cannot be overstated. They play a fundamental role in ensuring the quality of the final product, enhancing operational efficiency, and reducing maintenance costs. Manufacturers must invest in high-quality moulds and leverage technological advancements in their production processes to stay competitive in today's dynamic market. The future of tube manufacturing lies in the hands of those who recognize the significance of durable moulds and their contribution to overall success in the industry.