[Shear&butt welder]The Advantages and Applications of Shear & Butt Welder Technology in Modern Manufacturing Processes
News 2025-1-28
****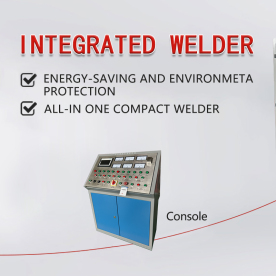
The Advantages and Applications of Shear & Butt Welder Technology in Modern Manufacturing Processes
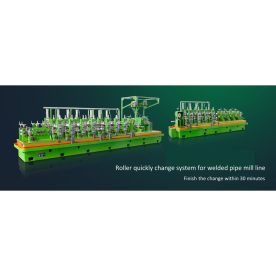
The Advantages and Applications of Shear & Butt Welder Technology in Modern Manufacturing Processes
Shear welding involves the joining of materials through the application of high shear forces, which eliminate surface contaminants and promote atomic bonding. This technique is particularly effective for joining thin materials, as it allows for precise control over the weld's depth and width. On the other hand, butt welding is a process where two pieces of metal are placed adjacent to each other and heated until they reach a molten state. This allows the edges of the metal pieces to fuse together, creating a strong bond once cooled.
Both shear and butt welding are widely used in various manufacturing settings due to their efficiency and ability to create high-quality welds. This has led to the development of specialized equipment, namely the shear & butt welder, which combines both techniques into a single, streamlined process.
Functionality of Shear & Butt Welders
Shear & butt welders utilize advanced technology to ensure precise, repeatable and efficient welds. These machines typically consist of hydraulic or pneumatic actuators that apply the necessary force to the workpieces. The process is often fully automated, allowing for consistent weld quality while minimizing the potential for human error. By controlling parameters such as temperature, pressure, and time, the shear & butt welder delivers optimal results with a minimal amount of distortion to the materials involved.

The Advantages and Applications of Shear & Butt Welder Technology in Modern Manufacturing Processes
Advantages of Shear & Butt Welding
1. **High-Quality Welds**: Shear & butt welding results in strong, seamless joints that exhibit minimal weld defects. The elimination of filler materials also means that the final product retains the original properties of the metals being joined, ensuring maximum strength and durability.
2. **Speed and Efficiency**: The automation involved in shear & butt welding significantly reduces the time required to complete welding tasks. This efficiency translates into increased production rates and reduced labor costs for manufacturers, making it an economically attractive option.
3. **Minimal Distortion**: Unlike some traditional welding processes that can cause significant warping or distortion due to heat, shear & butt welding minimizes these effects. This characteristic is especially beneficial for industries where dimensional accuracy is critical.
4. **Environmentally Friendly**: The process typically produces less waste compared to other welding techniques since no filler materials are used. Moreover, cleaner welds require less post-processing, thereby reducing the environmental impact associated with manufacturing processes.
Applications of Shear & Butt Welders
Due to their numerous advantages, shear & butt welders are employed across various industries. Some notable applications include:
- **Automotive**: In automotive manufacturing, shear & butt welders are used to join components such as chassis, frames, and fuel tanks. The durability of the welds enhances vehicle safety and performance.
- **Aerospace**: The aerospace industry benefits significantly from the high-quality welds produced by shear & butt welders. Critical components such as wings and fuselage sections require meticulous attention to detail, which this technology provides.
- **Construction**: In construction, shear & butt welders join structural steel elements and reinforcing bars, ensuring the integrity and strength of buildings and bridges.
- **Electronics**: For manufacturers of electronic devices, shear & butt welders can bond components like circuit boards without damaging sensitive parts.
Conclusion
The shear & butt welder has established itself as a vital tool in modern manufacturing. With advantages including high welding quality, speed, efficiency, minimal distortion, and environmental friendliness, this technology is perfectly suited for a wide array of applications. As industries continue to seek ways to optimize production while maintaining stringent quality standards, the role of shear and butt welding will only become more prominent in the years to come. Embracing this advanced welding technology not only boosts productivity but also sets a foundation for innovative manufacturing solutions.