[Solid state HF welder for metal processing]Exploring the Advantages and Applications of Solid State HF Welder for Metal Processing in Modern Manufacturing Industries
News 2025-1-28
**Introduction**
In today's ever-evolving industrial landscape, precision and efficiency are paramount. As manufacturers strive to improve their processes for better product quality, reducing production time and waste has become increasingly crucial. One of the cutting-edge technologies making a significant impact in metal processing is the solid state high-frequency (HF) welder. This article delves into the advantages and applications of solid state HF welders, their mechanism of operation, and their role in modern manufacturing.
**Understanding Solid State HF Welding Technology**
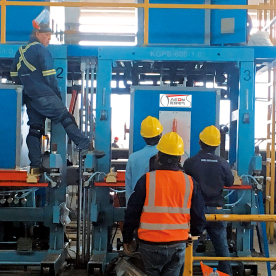
Exploring the Advantages and Applications of Solid State HF Welder for Metal Processing in Modern Manufacturing Industries
The solid state HF welder operates by passing electric current through the workpieces, which leads to localized heating. This rapid heating process ensures that the metal reaches its melting point quickly, allowing for strong and durable welds. One of the significant aspects of solid state HF welding is its ability to produce clean and aesthetically pleasing joints without introducing excessive heat-affected zones (HAZ).
**Advantages of Solid State HF Welders**
1. **Increased Efficiency**: Solid state HF welders are designed for high-speed operations, drastically reducing cycle times compared to traditional welding techniques. They can quickly weld thin sheets of metal, making them especially useful for industries where speed is crucial.
2. **Energy Savings**: The solid-state design minimizes energy consumption, as these welders operate with greater efficiency. They convert a higher percentage of the input power into usable energy for the welding process, resulting in lower operational costs.
3. **Reduced Maintenance**: With fewer moving parts and the elimination of vacuum tubes, solid state HF welders require significantly less maintenance than their predecessors. This reliability reduces downtime, leading to better productivity and cost savings for manufacturers.
4. **Versatility**: Solid state HF welders are adept at handling various materials, including aluminum, stainless steel, copper, and other metals. Additionally, they are suitable for various applications such as welding, brazing, and even soldering.
5. **Enhanced Control**: The solid state technology allows for precise control over the welding parameters, including power output and frequency. This control ensures the ability to tailor the welding process to the specific requirements of different materials and applications.
**Applications in Metal Processing**
Solid state HF welders find extensive use across various industries due to their adaptability and efficiency.
1. **Automotive Industry**: The automotive sector utilizes solid state HF welding for joining components such as battery packs, fuel tanks, and other assemblies. This technique ensures strong, lightweight connections that enhance vehicle performance and safety.
2. **Electronics Manufacturing**: In the electronics industry, solid state HF welders are instrumental in assembling delicate components. This method guarantees high-quality welds without damaging sensitive materials, thereby preserving the integrity of electronic devices.
3. **Aerospace**: The aerospace industry demands precision and reliability. Solid state HF welders are employed for assembling aircraft parts, ensuring that joints can withstand extreme conditions while maintaining low weight.
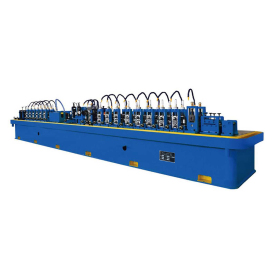
Exploring the Advantages and Applications of Solid State HF Welder for Metal Processing in Modern Manufacturing Industries
5. **Packaging**: In the manufacturing of metal packaging, solid state HF welding is used to create strong seals that enhance product safety and shelf life. This application is particularly important in food and pharmaceutical industries.
**Conclusion**
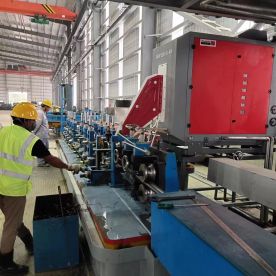