[Automatic ERW tube mill equipment]Exploring the Innovations and Benefits of Automatic ERW Tube Mill Equipment in Modern Manufacturing Processes
News 2025-1-27
****In the world of manufacturing, efficiency and precision are critical factors that can dictate the success of a production line. One technology that has significantly transformed the landscape is the Automatic ERW (Electric Resistance Welded) Tube Mill Equipment. This innovation offers various advantages for manufacturers, enabling them to produce high-quality tubes with reduced operational costs and enhanced productivity.
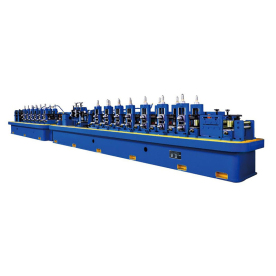
Exploring the Innovations and Benefits of Automatic ERW Tube Mill Equipment in Modern Manufacturing Processes
Electric Resistance Welding is a process used to produce tubes and pipes with seamless integrity. The ERW tube mills operate by passing a continuous strip of metal through a series of rollers and heating it using electrical resistance until the edges meet. A welding mechanism then fuses the edges together, creating a strong bond without the need for filler materials. This process is ideal for producing various steel tubing applications, including structural tubing, automotive components, and industrial pipes.
The Evolution of Automatic ERW Tube Mill Equipment
Automatic ERW tube mill equipment has evolved considerably over the years, driven by the demands for higher production efficiency, improved product quality, and better energy management. Unlike traditional ERW setups that require significant manual intervention, automatic systems integrate advanced technologies for more streamlined operations.
The latest automatic ERW tube mills feature programmable logic controllers (PLCs) and sophisticated software that allow for real-time monitoring and adjustments. These systems can automatically adjust operating parameters like speed, temperature, and pressure based on the material being processed. The automated approach minimizes human error and ensures a more consistent product output.
Key Features of Automatic ERW Tube Mill Equipment
1. **High Production Rates**: Automatic ERW tube mills are designed for high-speed production. Capable of operating continuously, these machines can significantly reduce cycle times, allowing manufacturers to meet increased demand without sacrificing quality.
2. **Precision and Consistency**: Automation ensures that each welded joint meets stringent quality standards. Advanced sensors and monitoring systems detect inconsistencies and allow for real-time corrections, reducing scrap rates and ensuring that every tube produced meets specifications.
3. **Versatility**: Modern automatic ERW tube mills can handle a variety of materials and tube sizes. The flexibility in operations enables manufacturers to cater to diverse industry needs without investing in separate machinery for each production requirement.
4. **Reduced Labor Costs**: With automation taking over the more tedious aspects of the production process, the requirement for manual labor decreases. This reduction in labor translates to lower overall operational costs and the ability to allocate skilled workers to more complex, value-added tasks.
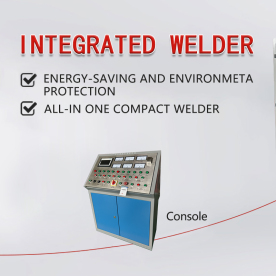
Exploring the Innovations and Benefits of Automatic ERW Tube Mill Equipment in Modern Manufacturing Processes
The Benefits of Investing in Automatic ERW Tube Mill Equipment
Investing in automatic ERW tube mill equipment is advantageous for manufacturers looking to scale operations. The initial capital expenditure may be substantial; however, the long-term benefits often outweigh the upfront costs. Here are some compelling reasons for manufacturers to consider this technology:
1. **Increased Competitiveness**: With enhanced production capabilities, manufacturers can offer more competitive pricing and faster turnaround times, giving them an edge in the market.
2. **Enhanced Product Quality**: Precision welding and control over the production process ensure that the final product is of high quality, meeting industry standards and customer expectations.
3. **Improved Return on Investment (ROI)**: As production costs decrease and output increases, manufacturers can expect a quicker ROI, further compelling the business case for adopting automatic ERW tube mills.
4. **Adaptability to Market Changes**: These advanced machines can be readily adjusted to meet changing customer demands, making it easier for businesses to pivot in response to market needs.

Exploring the Innovations and Benefits of Automatic ERW Tube Mill Equipment in Modern Manufacturing Processes
The adoption of automatic ERW tube mill equipment marks a significant advancement in the manufacturing sector. By integrating automation into the production process, manufacturers not only enhance efficiency and precision but also position themselves for future growth in an increasingly competitive landscape. As technology continues to evolve, the potential for further improvements in automatic ERW tube mills will undoubtedly unlock new possibilities for manufacturers worldwide, paving the way for innovation and excellence in the tubing industry.