[High frequency welder equipment]Understanding High Frequency Welder Equipment: How it Enhances Welding Precision and Efficiency in Modern Manufacturing
News 2025-1-26
In the realm of modern manufacturing, the importance of precision and efficiency cannot be overstated. With the introduction of advanced welding technologies, high frequency welder equipment has emerged as a game-changer for industries requiring reliable and high-quality welding processes. This article delves into what high frequency welders are, how they work, their applications, and the benefits they bring to various manufacturing sectors.
What is High Frequency Welder Equipment?
High frequency welding is a welding process that employs high frequency electrical currents to heat the materials being welded. Typically, the equipment consists of a power supply that generates high frequency signals, electrodes to transfer the current to the materials, and a workpiece holder that secures the components in place during the welding process. This method is particularly effective for welding thermoplastics and thin metals, making it ideal for a wide variety of applications.
How Does High Frequency Welding Work?
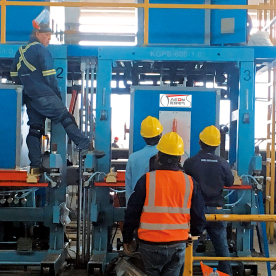
Understanding High Frequency Welder Equipment: How it Enhances Welding Precision and Efficiency in Modern Manufacturing
1. **Preparation**: The materials that need to be welded are carefully prepared. This includes ensuring clean surfaces, proper alignment, and the right physical properties for optimal welding.
2. **Electrode Contact**: The electrodes of the high frequency welder come into contact with the material to be welded. The equipment generates high frequency electrical currents that flow through the electrodes, producing heat at the interface of the materials.
3. **Heating and Bonding**: As the high frequency current flows through the materials, resistance heating occurs, leading to localized melting of the surfaces. Once the materials reach their melting point, they bond together when sufficient pressure is applied.
4. **Cooling**: After the welding process is complete, the materials are allowed to cool down in order to solidify the weld joint. This cooling process can be controlled to ensure the integrity and strength of the weld.
Applications of High Frequency Welder Equipment
High frequency welding finds its applications across a variety of industries due to its versatility:
- **Plastic Industry**: High frequency welding is widely used for bonding plastic materials, such as in the production of inflatable products like toys, air mattresses, and watercraft. It also plays a significant role in manufacturing coated fabrics and geotextiles.
- **Automotive Sector**: In the automotive industry, high frequency welders are utilized to create resilient and reliable welds for components like wiring harnesses and other assemblies that require a strong bond.
- **Aerospace Industry**: The precise control offered by high frequency welders makes them suitable for the aerospace sector, where safety and quality are paramount. Critical components must withstand extreme conditions, and high frequency welding ensures robust joints.
- **Medical Equipment**: In the medical industry, high frequency welding is employed in the production of items such as surgical instruments, catheters, and medical bags. The clean and precise welding process is crucial for ensuring product safety and effectiveness.
Advantages of Using High Frequency Welder Equipment
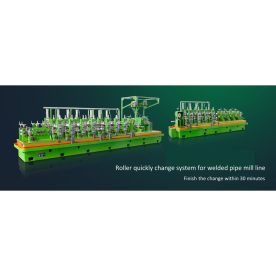
Understanding High Frequency Welder Equipment: How it Enhances Welding Precision and Efficiency in Modern Manufacturing

Understanding High Frequency Welder Equipment: How it Enhances Welding Precision and Efficiency in Modern Manufacturing
- **Efficiency**: High frequency welding is notably faster than conventional welding methods. The process takes mere seconds, reducing production time and increasing output.
- **Precision**: The ability to control the heat and pressure applied during welding ensures high-quality welds with minimal defects. This precision is essential in industries where even slight imperfections can lead to failures.
- **Environmentally Friendly**: Unlike other welding techniques that may emit harmful fumes or use hazardous materials, high frequency welding is cleaner and often requires less energy.
- **Cost-Effectiveness**: While the initial investment in high frequency welder equipment may be higher, the improved efficiency and reduced material waste lead to long-term savings for manufacturers.
Conclusion
High frequency welder equipment is leading the way in modern welding technology, offering manufacturers enhanced precision, efficiency, and reliability. With its wide range of applications across various sectors, it is clear that high frequency welding is not just a trend, but a necessary tool for those looking to remain competitive in today’s fast-paced manufacturing landscape. As industries continue to evolve, the demand for innovative welding solutions like high frequency welding will undoubtedly grow, paving the way for even more advancements in the field.