[Automatic Solid state HF welder]Revolutionizing Metal Joining Processes: The Role of Automatic Solid State HF Welder in Modern Manufacturing
News 2025-1-24
****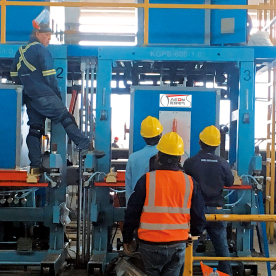
Revolutionizing Metal Joining Processes: The Role of Automatic Solid State HF Welder in Modern Manufacturing
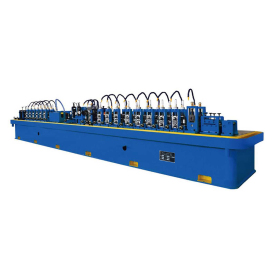
Revolutionizing Metal Joining Processes: The Role of Automatic Solid State HF Welder in Modern Manufacturing
One of the primary advantages of the Automatic Solid State HF Welder is its ability to produce high-strength welds with minimized thermal distortion. Traditional welding processes often result in high heat-affected zones (HAZ), which can weaken the surrounding material and compromise the structural integrity of the finished product. In contrast, the solid-state method keeps the heat concentrated at the joint, effectively reducing HAZ and maintaining optimal material properties.
Moreover, the Automatic Solid State HF Welder offers a remarkable increase in automation and consistency. In modern manufacturing setups, automation has become essential for ensuring repeatability and quality control. These welders are designed to integrate seamlessly into automated production lines, thereby allowing for unattended operation. This capability not only enhances productivity but also reduces labor costs associated with manual welding processes.
The versatility of the Automatic Solid State HF Welder further contributes to its growing popularity. These welders are suitable for a wide range of metal types, including copper, aluminum, and various alloys. In industries like automotive, where complex assemblies with varied materials are common, the ability to adapt to different metals without needing substantial modification to the welding setup gives manufacturers a significant edge.
One of the most remarkable features of the Automatic Solid State HF Welder is its energy efficiency. Traditional welding processes can consume substantial amounts of energy, leading to higher operational costs and increased environmental impacts. Solid-state HF welding, on the other hand, minimizes energy consumption by generating heat directly at the weld interface, resulting in reduced overall energy usage. This emphasis on sustainability aligns with the growing trend of environmentally conscious manufacturing practices, allowing companies to enhance their green credentials.
The technology behind the Automatic Solid State HF Welder is centered around sophisticated control systems that monitor and adjust the welding parameters in real-time. This feature ensures that each weld achieves maximum strength while minimizing the risk of defects. Additionally, feedback systems provide data that can be used for further analysis, contributing to continuous improvement in production processes.
In terms of applications, the Automatic Solid State HF Welder is making significant inroads in industries such as electronics manufacturing, particularly for tasks like joining components in circuit boards or creating wire connections within devices. The medical device sector is also taking advantage of this technology, where precision and reliability are paramount. Beyond these sectors, the increased adoption of the Automatic Solid State HF Welder is expected to create new opportunities in fabrication works that require high-quality welds.
The investment in an Automatic Solid State HF Welder may seem substantial at first but is often justified through the long-term savings in energy, labor, and material costs. Furthermore, as industries continue to embrace automation and seek methods to enhance product quality, the demand for these innovative welders is anticipated to increase.
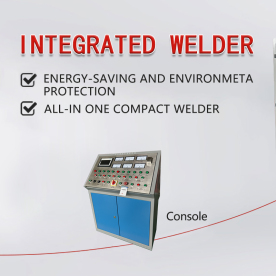