[Precision Mould for Tube Mills]The Importance of Precision Mould for Tube Mills in Enhancing Manufacturing Efficiency and Product Quality
News 2025-1-22
In the ever-evolving landscape of manufacturing, where precision and efficiency are paramount, the role of specific tools and technologies cannot be overstated. Among these, precision moulds for tube mills have emerged as pivotal components that significantly enhance production capabilities. Tube mills, which are essential for the creation of circular tubes from metal sheets, require high-quality moulds to ensure the seamless formation of products. This article delves into the importance of precision moulds for tube mills, exploring their design, benefits, and impact on overall manufacturing efficiency and product quality.
Precision and accuracy are non-negotiable in modern manufacturing processes, especially in industries such as automotive, aerospace, and construction, where specifications are stringent. Tube mills rely on precision moulds to dictate the shape and dimensions of tubes being produced. When precision moulds are employed, manufacturers can achieve tighter tolerances, ensuring that the final products meet the exacting standards required in various applications. This precision not only enhances the quality of the tubes produced but also reduces the need for rework—saving time, resources, and costs.
One of the primary advantages of utilizing precision moulds in tube mills is their role in optimizing production efficiency. Traditional moulds can suffer from wear and tear, leading to inconsistent product quality and potential downtimes. However, precision moulds are crafted from high-grade materials designed to withstand rigorous manufacturing conditions. By investing in precision moulds, manufacturers can extend the lifespan of their tooling, minimizing downtime and maximizing productivity. This longevity of equipment goes hand-in-hand with reduced maintenance costs, further contributing to economic efficiency.
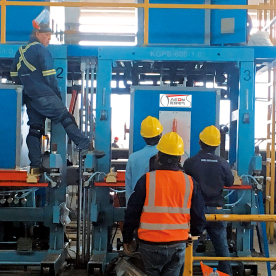
The Importance of Precision Mould for Tube Mills in Enhancing Manufacturing Efficiency and Product Quality
Moreover, precision moulds for tube mills facilitate continuous improvement in production processes. With real-time data analysis and monitoring becoming increasingly common in manufacturing, the integration of precision moulds allows firms to gather critical data regarding production performance. This information can be used to identify bottlenecks, inefficiencies, or areas for optimization. Manufacturers can adapt their processes based on analytical insights drawn from using precision moulds, leading to an iterative process of refinement that furthers product quality and manufacturing efficiency over time.
While the focus on efficiency and durability of precision moulds is vital, it is equally important to consider their environmental impact. As industries move toward sustainable practices, precision moulds play a significant role in facilitating eco-friendly manufacturing. By enabling more precise cutting and forming of materials, less waste is generated during the production process. Additionally, the longevity of these moulds contributes to a reduction in material consumption over time, supporting an organization’s sustainability goals.
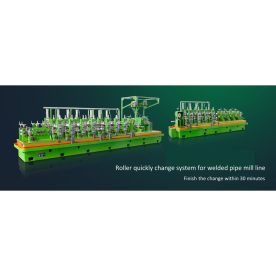
The Importance of Precision Mould for Tube Mills in Enhancing Manufacturing Efficiency and Product Quality
