[All-in-one High Frequency Welder for Automotive Industry]Revolutionizing the Automotive Industry: Exploring the Benefits of an All-in-One High Frequency Welder for Enhanced Manufacturing Efficiency
News 2025-1-20
In the fast-paced world of the automotive industry, technological advancements play a crucial role in enhancing production efficiency, reducing costs, and improving the overall quality of vehicles. One of the most significant innovations to emerge in recent years is the All-in-One High Frequency Welder. This versatile tool has transformed traditional welding processes, making them faster, more reliable, and adaptable to the diverse needs of automotive manufacturing.
At its core, an All-in-One High Frequency Welder utilizes electromagnetic frequency to join materials with precision and speed. Unlike conventional welding techniques like MIG or TIG, this technology operates by generating high-frequency current that induces rapid heating in conductive materials, allowing them to bond without the need for excessive external heat or pressure. This results in minimal thermal distortion and a cleaner workspace, making it ideal for various applications in the automotive sector.
The benefits of using an All-in-One High Frequency Welder in the automotive industry are manifold. First and foremost, it significantly increases production efficiency. Traditional welding methods can be time-consuming, requiring meticulous setup and manual intervention. However, the High Frequency Welder streamlines the process, reducing cycle times and enabling manufacturers to produce a higher volume of vehicles within the same timeframe. This efficiency is not only advantageous for production but also for meeting the ever-increasing demand in a highly competitive market.
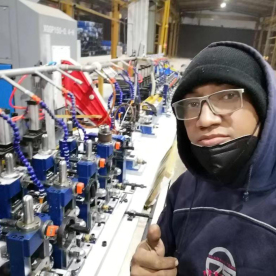
Revolutionizing the Automotive Industry: Exploring the Benefits of an All-in-One High Frequency Welder for Enhanced Manufacturing Efficiency
Another significant aspect of the All-in-One High Frequency Welder is the reduction in scrap and waste materials. Traditional welding processes often produce excess material that must be cleaned up or discarded, leading to increased costs and environmental implications. However, with high-frequency welding, the precise heating and joining of materials minimize waste, contributing to more sustainable manufacturing practices. As the automotive industry moves toward greener production methods, this efficiency helps companies align with global sustainability goals.
In terms of safety, the design and operation of the All-in-One High Frequency Welder provide improvements over traditional methods. High-frequency welding generates less heat in the surrounding areas, reducing the risk of burns and the potential for fire hazards. Additionally, the automated nature of the welding process means that workers can operate the equipment from a safe distance, further minimizing their exposure to risk.
Automotive manufacturers must also consider the pressure for compliance with stringent quality control standards. The All-in-One High Frequency Welder offers enhanced process control, with the ability to monitor and adjust parameters in real-time. This capability ensures that every weld is consistent and meets or exceeds industry standards. By producing high-quality, reliable welds, manufacturers can reduce recalls and warranty claims, ultimately saving costs and fostering customer satisfaction.
Furthermore, the integration of smart technology into the All-in-One High Frequency Welder allows for data collection and analysis that can drive continuous improvement in manufacturing processes. Real-time insights into production metrics enable manufacturers to identify bottlenecks, optimize workflows, and refine operational strategies based on concrete evidence.
As the automotive industry continues to evolve, driven by factors such as electrification, automation, and the demand for lightweight structures, the All-in-One High Frequency Welder stands out as a transformative solution. It not only enhances production capabilities but also promotes a shift toward innovative designs that define the future of transportation.
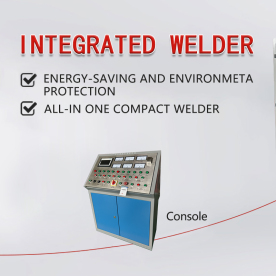
Revolutionizing the Automotive Industry: Exploring the Benefits of an All-in-One High Frequency Welder for Enhanced Manufacturing Efficiency
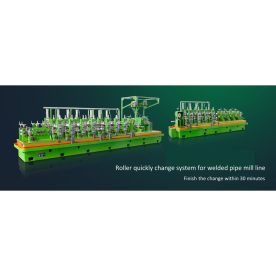