[Precision Tube making equipment]The Future of Manufacturing: How Precision Tube Making Equipment is Revolutionizing Industrial Processes
News 2025-1-20
****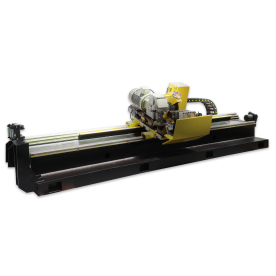
The Future of Manufacturing: How Precision Tube Making Equipment is Revolutionizing Industrial Processes
The significance of precision in manufacturing cannot be overstated. Tubes and pipes are integral components in various applications, serving critical functions such as fluid transport, structural support, and even aesthetic detailing. For example, in the aerospace industry, tubes must sustain substantial pressure while remaining lightweight and resistant to environmental factors. In automotive manufacturing, precision in tubing can lead to improvements in fuel efficiency and overall vehicle performance. Given these requirements, manufacturers are increasingly turning to precision tube making equipment to meet their high standards.
Precision tube making equipment is engineered to produce tubes with exceptional accuracy. Modern machinery employs advanced technologies such as CNC (Computer Numerical Control) processes, laser cutting, and precision welding techniques to ensure that each tube conforms to the required specifications. This level of automation not only reduces the likelihood of human error but also increases production speed, enabling manufacturers to respond swiftly to fluctuating market demands.
One of the standout features of precision tube making equipment is its versatility. It can produce a wide range of tube diameters, wall thicknesses, and materials, including stainless steel, aluminum, copper, and even specialized polymer composites. This adaptability makes it a valuable addition to any manufacturing facility aiming to offer diverse products or cater to niche markets. Companies can adjust their production lines to create tubes for different applications, minimizing downtime and expenditure associated with retooling.
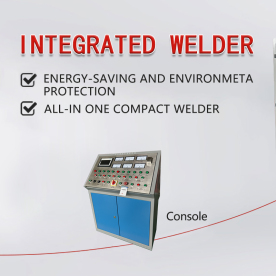
The Future of Manufacturing: How Precision Tube Making Equipment is Revolutionizing Industrial Processes
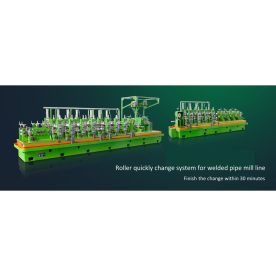
The Future of Manufacturing: How Precision Tube Making Equipment is Revolutionizing Industrial Processes
Additionally, precision tube making equipment supports the growing trend of customization in manufacturing. As customers demand increasingly tailored solutions that cater to their specific needs, manufacturers rely on the flexibility offered by advanced tube making equipment. These machines can quickly adapt to produce custom lengths, diameters, and shapes without extensive reconfiguration, empowering businesses to meet unique customer requirements promptly.
Despite the many advantages that precision tube making equipment offers, its implementation does present certain challenges. The initial investment required for advanced machinery can be significant. However, this is often outweighed by the long-term benefits of enhanced efficiency, reduced material waste, and improved product quality. Moreover, workforce training on advanced technologies becomes essential to fully utilize the capabilities of the equipment.
In conclusion, precision tube making equipment is not merely a component of modern manufacturing; it is a catalyst for industry innovation. As manufacturers continue to embrace automation and advanced technologies, the impact of precision tube making will only become more profound. Ensuring that products meet exacting standards while promoting sustainability and efficiency is the future of manufacturing, where precision tube making machinery stands as a cornerstone. In a world increasingly dependent on high-quality materials and components, companies that invest in these technological advancements will undoubtedly enhance their competitiveness and market presence.