[High-efficiency ERW tube mill]Maximizing Production with High-Efficiency ERW Tube Mills: Revolutionizing the Manufacturing Landscape in the Steel Industry
News 2025-1-20
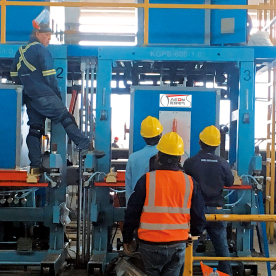
Maximizing Production with High-Efficiency ERW Tube Mills: Revolutionizing the Manufacturing Landscape in the Steel Industry
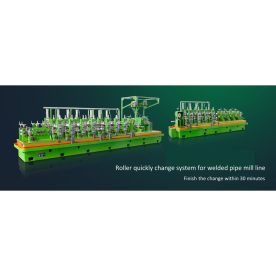
Maximizing Production with High-Efficiency ERW Tube Mills: Revolutionizing the Manufacturing Landscape in the Steel Industry
One of the key benefits of high-efficiency ERW tube mills is their ability to produce tubes at unprecedented speeds. Traditional tube mills often face inefficiencies due to mechanical limitations and the time-consuming nature of conventional welding techniques. In contrast, modern high-efficiency models can operate at significantly higher speeds, reducing cycle times and increasing throughput. Manufacturers can thus meet growing market demands without compromising quality or incurring excessive costs associated with labor and energy consumption.
Another advantage of these state-of-the-art mills is the reduction in material waste. High-efficiency ERW tube mills are designed to optimize the utilization of raw materials. By precisely controlling the welding parameters and maintaining ideal temperatures, manufacturers can produce tubes with minimal scrap. This reduction in waste not only contributes to cost savings but also enhances the sustainability of manufacturing operations, aligning with global trends toward environmental responsibility.
Technological advancements play a pivotal role in the high efficiency of these mills. Many modern ERW tube mills feature sophisticated automation and control systems that allow for real-time monitoring and adjustments. This level of automation ensures consistency in product quality while minimizing the need for manual intervention. Operators can effectively manage the entire production process from a centralized control station, enhancing oversight and efficiency. Additionally, advancements in sensors and data analytics enable predictive maintenance, reducing downtimes and further optimizing production schedules.
The flexibility of high-efficiency ERW tube mills is another critical aspect that appeals to manufacturers. These mills can be easily adapted to produce tubes of various sizes and specifications, catering to diverse market needs. This adaptability is vital in an era where customization and quick response times are essential for staying competitive. Manufacturers can shift production lines to meet specific demands without significant downtime or investment in new equipment.

Maximizing Production with High-Efficiency ERW Tube Mills: Revolutionizing the Manufacturing Landscape in the Steel Industry
Despite the apparent advantages, manufacturers must carefully evaluate their needs before transitioning to high-efficiency ERW tube mills. Factors such as production volume, product specifications, and existing infrastructure should guide decisions to ensure that investments are profitable. Additionally, proper training for personnel operating advanced machinery is crucial to maximizing the capabilities of high-efficiency mills and minimizing the risk of operational issues.
In conclusion, the rise of high-efficiency ERW tube mills is revolutionizing the steel manufacturing landscape. By maximizing production capabilities, minimizing waste, and enhancing flexibility, these advanced systems offer manufacturers a viable pathway to remain competitive in an increasingly demanding market. As technology continues to evolve, the adoption of high-efficiency ERW tube mills will likely accelerate, further solidifying their integral role in the future of tube manufacturing. Embracing these innovations will not only benefit individual manufacturers but also contribute to a more sustainable and efficient steel industry as a whole.