[Solid state HF welder]Exploring the Advantages and Applications of Solid State HF Welders in Modern Manufacturing Processes
News 2025-1-19
In recent years, the manufacturing sector has witnessed rapid advancements in technology, leading to the evolution of various welding techniques. One of the most revolutionary developments in this field is the solid state high-frequency (HF) welder. These advanced welding systems have rapidly become indispensable tools across numerous industries due to their precision, efficiency, and versatility. In this article, we will explore the advantages and applications of solid state HF welders, demonstrating their value in modern manufacturing processes.
**Understanding Solid State HF Welding Technology**
Solid state HF welding is a process that primarily utilizes high-frequency electrical energy to create a weld between two metal components. Unlike traditional welding methods that often require bulky transformers and vacuum tubes, solid state HF welders use semiconductor devices for power conversion. This fundamental shift in design not only reduces the size and weight of the equipment but also enhances its operational efficiency and reliability.
The technology behind solid state HF welders allows for precise control over welding parameters, including frequency, current, and pressure. This high level of control is essential for achieving the desired weld quality and consistency, making solid state HF welding particularly well-suited for fine and intricate applications.
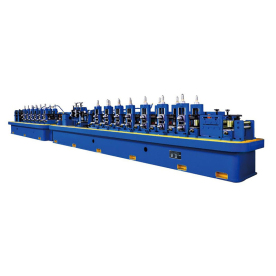
Exploring the Advantages and Applications of Solid State HF Welders in Modern Manufacturing Processes
1. **Efficiency and Speed**: Solid state HF welders are known for their rapid heating capabilities. The welding process can be completed in a matter of seconds, significantly reducing cycle times and increasing production rates. This efficiency is particularly advantageous in high-volume manufacturing settings, where time is a critical factor.
2. **Energy Savings**: With reduced power consumption compared to traditional welders, solid state HF welders contribute to lower operational costs. The high-frequency technology minimizes energy losses, meaning that manufacturers can operate these systems at a fraction of the energy cost of their predecessors.
3. **Versatility**: Solid state HF welders can effectively join a wide range of materials, including metals, plastics, and composites. This adaptability is crucial in industries such as automotive, aerospace, and packaging, where different materials are often used in conjunction. The ability to work with varied materials makes solid state HF welding a valuable tool for manufacturers.
4. **Precision and Control**: The advanced control systems in solid state HF welders allow for fine adjustments to be made during the welding process. Manufacturers can set specific parameters that ensure a consistent weld quality, reducing the risk of defects that can lead to costly rework or scrap.
5. **Reduced Maintenance**: Traditional welding systems often suffer from the wear and tear of mechanical components and consumables. Solid state HF welders, with their few moving parts and robust semiconductor technology, report lower maintenance needs. This reliability translates to reduced downtime and enhanced productivity.
**Applications Across Industries**
The versatility and superior performance of solid state HF welders enable their application across various sectors. Here are some notable examples:
- **Automotive Industry**: In automotive manufacturing, solid state HF welders are utilized to join components such as wiring harnesses, trims, and even panel assemblies. The ability to create strong, reliable joints without damaging surrounding materials is crucial in this sector.
- **Packaging Industry**: Solid state HF welding is frequently used for sealing plastic packaging materials. The precision and speed of the weld help ensure that products are packaged securely and efficiently, preserving their quality and longevity.
- **Aerospace Applications**: In aerospace manufacturing, where weight and reliability are of utmost importance, solid state HF welders are used for joining components in lightweight structures. Their high degree of control and ability to work with composite materials make them ideal for this demanding industry.
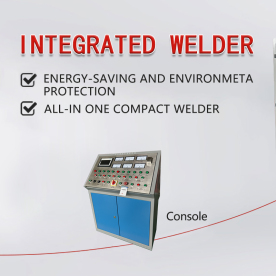
Exploring the Advantages and Applications of Solid State HF Welders in Modern Manufacturing Processes
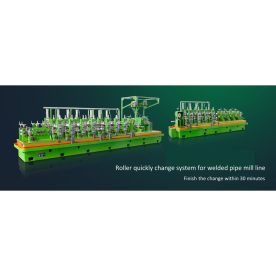
Exploring the Advantages and Applications of Solid State HF Welders in Modern Manufacturing Processes
In conclusion, solid state HF welders represent a significant advancement in welding technology, offering an array of benefits that align with the demanding requirements of modern manufacturing. Their efficiency, energy savings, versatility, and precision make them a vital asset in various industries. As technology continues to evolve, it is clear that solid state HF welding will play an increasingly pivotal role in shaping the future of manufacturing processes. Businesses looking to enhance their production capabilities and stay competitive would do well to consider the integration of solid state HF welders into their operations.