[Stainless steel pipe mill production line]Exploring the Innovations and Processes Behind a Modern Stainless Steel Pipe Mill Production Line
News 2025-1-19
****The stainless steel pipe mill production line is a marvel of modern engineering, transforming raw materials into high-quality stainless steel pipes used across various industries. This article delves into the intricacies of the production process, the technological advancements involved, and the significance of stainless steel pipes in today's market.
Understanding the Basics
Stainless steel pipes are made from an alloy of iron, chromium, nickel, and other elements, providing them with excellent corrosion resistance, strength, and durability. The stainless steel pipe mill production line is responsible for the manufacturing of these pipes through a series of meticulously coordinated steps. The processes involved can be broadly categorized into raw material preparation, pipe production, finishing, and quality control.
Raw Material Preparation
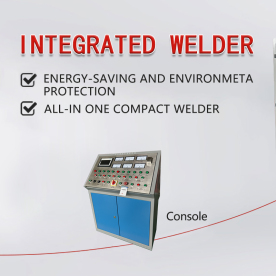
Exploring the Innovations and Processes Behind a Modern Stainless Steel Pipe Mill Production Line
After refining, the molten steel is cast into billets or slabs, which are solidified blocks of steel. This is a crucial step, as the consistency and purity of the steel directly affect the quality of the final pipes. Once cooled, these billets are transported to the next stage for shaping.
Pipe Production Process
The primary method for manufacturing stainless steel pipes in a mill involves two main processes: seamless pipe production and welded pipe production.
**Seamless Pipe Production**
In the seamless pipe production line, the billets are heated and pierced to create a hollow tube. This is achieved through a process known as rotary piercing, where a series of rollers deform the hot billet and form a hollow shape. The pipe is then elongated using a stretch-reducing mill, ensuring uniform wall thickness.
**Welded Pipe Production**
Conversely, welded pipes are produced by taking stainless steel plates or strips, which are first rolled into a cylindrical shape and then welded together. The welding process is essential in ensuring the integrity of the pipe. Strip edges are heated using high-frequency induction and then fused together to form a solid seam. After welding, the pipes undergo additional processing, such as smoothing the weld and testing for leaks.
Finishing Processes
Once the pipes are formed, they go through various finishing processes to enhance their surface properties and mechanical characteristics. Common finishing treatments include heat treatment, pickling, passivation, and polishing. Heat treatment improves the microstructure of stainless steel, enhancing its mechanical properties.
**Pickling and Passivation**
After welding, pipes can be covered with oxides and other contaminants that may affect corrosion resistance. Pickling involves treating the surface with acid solutions to remove these impurities. Passivation follows, wherein the pipe is exposed to a mild oxidizing solution to enhance its natural oxide layer, providing additional corrosion resistance.
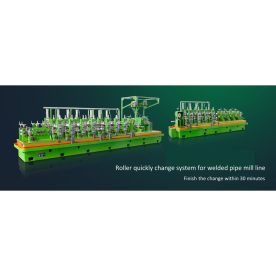
Exploring the Innovations and Processes Behind a Modern Stainless Steel Pipe Mill Production Line
In industries where aesthetic qualities are essential, polishing may be performed. This step enhances not only the appearance of the pipes but also contributes to their durability.
Quality Control
The final stage in the stainless steel pipe mill production line is quality control. Rigorous testing is conducted to ensure that the pipes meet the required specifications and industry standards. These tests can include dimensional checks, tensile strength testing, and non-destructive testing methods, such as ultrasonic or radiographic inspections. Ensuring the pipes are free from defects is crucial, as they often carry fluids under pressure in critical applications.

Exploring the Innovations and Processes Behind a Modern Stainless Steel Pipe Mill Production Line
The stainless steel pipe mill production line exemplifies the fusion of technology and craftsmanship. The attention to detail throughout the production process, from raw material selection to finishing and quality control, results in high-performance pipes suitable for a variety of applications, including construction, automotive, and energy sectors. As industries continue to evolve and demand higher-quality materials, the innovations in stainless steel production will undoubtedly play a significant role in meeting these needs for years to come.