[Mould for tube mill]Understanding the Importance of Mould for Tube Mill: A Comprehensive Guide to Enhancing Production Efficiency and Quality
News 2025-1-19
****In the ever-evolving world of manufacturing, the tube mill plays a crucial role in producing high-quality tubes used in various industries, from automotive to construction. Among the critical components of a tube mill is the mould, which shapes the raw material into the desired form. The significance of the mould for tube mill operations cannot be overstated. This article delves into the key aspects of moulds, their types, and their impact on tube mill efficiency and product quality.
Introduction to Tube Mills
A tube mill is a machine designed to produce metal tubes, primarily by rolling sheets or strips of material into cylindrical shapes. These mills work through a sequence of processes that include slitting, forming, welding, and final shaping. The quality of the final product relies heavily on the precision and design of the mould used during the manufacturing process.
What is a Mould in Tube Mills?
In the context of tube mills, a mould is a hollow structure that allows the molten or semi-molten material to take shape as it is processed. The mould not only controls the shape of the tube but also influences surface finish, wall thickness, and dimensional accuracy. The efficiency of a tube mill can largely depend on the design and condition of the mould used, making it an integral part of the manufacturing process.
Types of Moulds Used in Tube Mills
1. **Standard Moulds**: These are commonly used in tube mills for general-purpose applications. Standard moulds are typically designed for production runs and are built to accommodate certain dimensions and tolerances.
2. **Custom Moulds**: When production requires specific shapes or sizes, custom moulds are designed to meet these unique specifications. Custom moulds allow manufacturers to create specialized products that may not be possible with standard moulds.
3. **Adjustable Moulds**: Some tube mills utilize adjustable moulds that can change dimensions within a predetermined range. This flexibility allows for the production of various tube sizes without the need for complete mould replacement.
Importance of Mould Design and Quality
The design of the mould for a tube mill is paramount. A well-designed mould ensures:
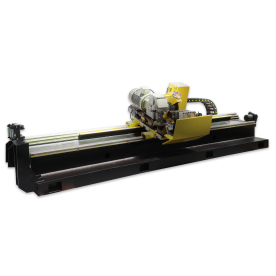
Understanding the Importance of Mould for Tube Mill: A Comprehensive Guide to Enhancing Production Efficiency and Quality
- **Surface Finish**: The quality of the mould surface directly affects the finish of the tube. A smooth mould surface results in better surface quality, reducing the need for further finishing processes.
- **Material Flow**: A good mould design facilitates better material flow, reducing defects such as inconsistencies in wall thickness or surface irregularities.
- **Heat Management**: Effective mould design considers heat distribution during the forming process, which can prevent warping or misalignment, enhancing product durability.
Maintenance of Moulds
Regular maintenance of moulds is critical to ensuring their longevity and functionality. Here are some essential maintenance tips:
- **Routine Inspections**: Inspect moulds regularly for signs of wear and tear. Early detection of issues can prevent more significant problems in production.
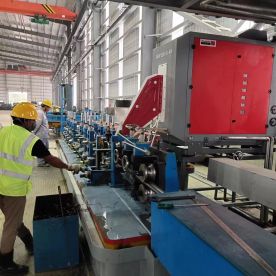
Understanding the Importance of Mould for Tube Mill: A Comprehensive Guide to Enhancing Production Efficiency and Quality
- **Repairs and Replacements**: Address any damage immediately. If moulds show excessive wear, it may be more economical to replace them rather than repair, especially in high-volume production environments.
Conclusion
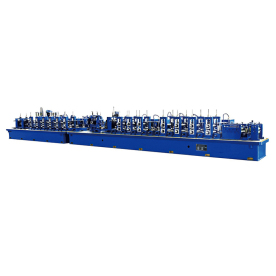