[Solid state high frequency welder]The Evolution and Advantages of Solid State High Frequency Welders in Modern Manufacturing Processes
News 2025-1-18
Introduction
In the rapidly evolving landscape of modern manufacturing, the demand for efficient and reliable welding techniques has never been higher. Among the various methods available, the solid state high frequency welder has emerged as a front-runner, offering unparalleled precision, speed, and energy efficiency. This article delves into the workings of solid state high frequency welders, their benefits, applications in various industries, and the factors driving their growing adoption.
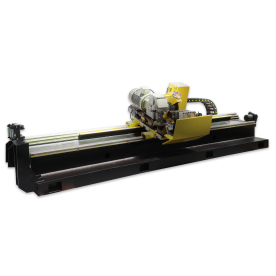
The Evolution and Advantages of Solid State High Frequency Welders in Modern Manufacturing Processes
Solid state high frequency welders utilize advanced semiconductor technology to generate high-frequency currents for welding processes. Unlike traditional tube welders that rely on high-voltage vacuum tubes, solid state welders use transistors and diodes to produce stable and consistent electrical power. This transition to solid-state technology brings numerous advantages, including improved energy efficiency, reduced maintenance needs, and enhanced control over the welding process.
High frequency welders operate by inducing high-frequency electromagnetic fields within a conductive workpiece, which heats the material to its melting point. This process is particularly effective for welding thin materials, making it a popular choice in industries such as automotive manufacturing, aerospace, and electrical engineering.
Advantages of Solid State High Frequency Welders
1. **Energy Efficiency**: One of the most significant advantages of solid state high frequency welders is their energy efficiency. Due to their ability to fine-tune power output, these welders minimize energy wastage during operations. This not only translates to lower electricity bills for manufacturers but also aligns with global sustainability efforts by reducing overall energy consumption.
2. **Reliability and Durability**: Solid state components are inherently more durable than traditional vacuum tubes. This durability means reduced maintenance and longer operational lifetimes for the equipment, significantly lowering the total cost of ownership. Manufacturers can benefit from fewer disruptions in production, leading to improved overall efficiency.
3. **Precision and Control**: Solid state high frequency welders provide advanced controls that allow for precise management of welding parameters. Features such as programmable power settings and automatic adjustments based on real-time feedback lead to consistent and high-quality welds. This level of control is crucial in industries where precision is non-negotiable, such as medical device manufacturing and electronics.
4. **Versatility**: These welders can handle a wide range of materials and thicknesses, making them versatile tools for different applications. From metals and plastics to composites, solid state high frequency welders can efficiently join various materials, catering to a broad spectrum of manufacturing requirements.
5. **Compact Design**: The solid state design is inherently more compact than traditional welding systems, allowing manufacturers to save valuable floor space in their facilities. This compactness aligns well with modern manufacturing practices, which often emphasize lean operations and efficient spatial arrangements.
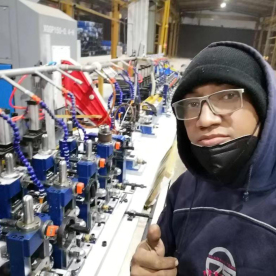
The Evolution and Advantages of Solid State High Frequency Welders in Modern Manufacturing Processes
Solid state high frequency welders are employed in numerous industries due to their versatility and efficiency. In the **automotive sector**, these welders are widely used for assembling various components, including exhaust systems and body panels. Their ability to handle thin materials effectively makes them ideal for modern vehicle designs that prioritize weight reduction.
In **aerospace**, where the quality of each weld can be a matter of safety, the precision offered by solid state high frequency welders is invaluable. These welders ensure that components are joined securely without compromising their structural integrity, vital for aircraft and spacecraft applications.
The **electrical engineering** field also benefits significantly from solid state high frequency welding technology. Manufacturers of electrical components like transformers, inductors, and circuit breakers utilize these welders to create reliable connections that can withstand high voltage and current loads.
Conclusion
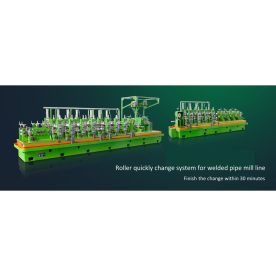