[Tube making machine for industrial applications]Revolutionizing Manufacturing Efficiency: How Tube Making Machines are Transforming Industrial Applications
News 2025-1-17
****In the rapidly evolving landscape of manufacturing, the quest for improved efficiency, reduced costs, and enhanced precision is a constant endeavor. At the forefront of this transformation are Tube Making Machines, which have become integral to various industrial applications. This article delves into the significance of tube making machines in industrial settings, their functionalities, benefits, and the technological advancements driving their evolution.
What are Tube Making Machines?
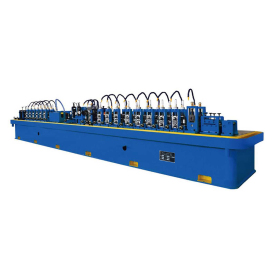
Revolutionizing Manufacturing Efficiency: How Tube Making Machines are Transforming Industrial Applications
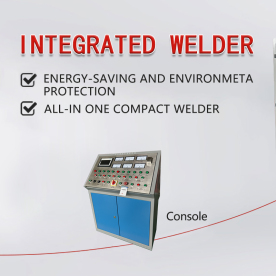
Revolutionizing Manufacturing Efficiency: How Tube Making Machines are Transforming Industrial Applications
The role of tube making machines in industrial applications is multifaceted. Firstly, they enable manufacturers to produce components that are crucial for structural integrity and functionality across various products. For instance, in the automotive sector, tubes are used for exhaust systems, fuel lines, and structural frames. Similarly, in the aerospace industry, precise tube manufacturing is essential for ensuring safety and performance in aircraft systems.
Another critical aspect is the customization that tube making machines allow. Manufacturers can produce tubes in various sizes, shapes, and materials, catering to the specific demands of different industries. This flexibility is especially vital in today’s market, where companies strive to innovate and meet the unique requirements of their customers.
Modern Technological Advancements
Recent technological advancements have significantly enhanced the capabilities of tube making machines, making them more efficient and user-friendly. Automation is a prime example; many modern machines come equipped with advanced control systems that reduce the need for manual intervention. This not only speeds up the production process but also minimizes the risk of human error, leading to more consistent quality in the finished products.
Moreover, the integration of Industry 4.0 principles has paved the way for smarter manufacturing. Tube making machines can now be connected to the Internet of Things (IoT), allowing real-time monitoring and data analysis. Manufacturers can track production metrics, allowing for predictive maintenance and reducing downtime by identifying potential issues before they escalate.

Revolutionizing Manufacturing Efficiency: How Tube Making Machines are Transforming Industrial Applications
1. **Increased Efficiency**: By automating the manufacturing process and optimizing production workflows, tube making machines significantly increase operational efficiency. This leads to higher output rates and faster turnaround times, crucial in a competitive market.
2. **Cost Savings**: Although the initial investment in advanced tube making machinery can be significant, the long-term savings often outweigh the costs. By reducing material waste and improving energy efficiency, manufacturers can achieve substantial cost reductions over time.
3. **Improved Quality**: The precision and consistency offered by modern tube making machines result in higher-quality products. Consistent tolerances and better surface finishes translate into more reliable components that meet industry standards.
4. **Sustainability**: Many tube making machines are designed with sustainability in mind, utilizing materials and processes that reduce environmental impact. For instance, some machines can recycle scrap materials produced during the manufacturing process, contributing to a more sustainable production cycle.
Conclusion
The landscape of industrial manufacturing is continually changing, driven by the need for greater efficiency, customization, and sustainability. Tube making machines are at the forefront of this evolution, serving as a backbone for multiple industries. Their ability to streamline production, increase quality, and minimize costs makes them invaluable assets in today’s manufacturing environment.
As technology advances, tube making machines are expected to become even more sophisticated, incorporating artificial intelligence, machine learning, and enhanced automation features. For businesses looking to maintain a competitive edge, investing in modern tube making technology is not just an option; it is a necessity. Embracing these innovations will undoubtedly pave the way for a more efficient and sustainable manufacturing future.