[Stainless steel pipe mill production line]An In-Depth Exploration of the Stainless Steel Pipe Mill Production Line: Innovations, Techniques, and Future Trends
News 2025-1-16
**Introduction**
In today's industrial landscape, the demand for high-quality stainless steel pipes is on the rise, driven by various sectors such as construction, automotive, and manufacturing. The stainless steel pipe mill production line plays a pivotal role in meeting this demand. This article will delve into the intricacies of the stainless steel pipe mill production line, highlighting its components, processes, innovations, and the future of stainless steel pipe production.
**Components of a Stainless Steel Pipe Mill Production Line**
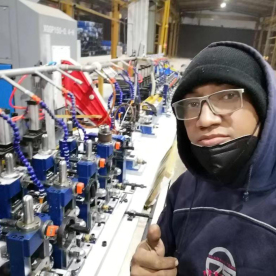
An In-Depth Exploration of the Stainless Steel Pipe Mill Production Line: Innovations, Techniques, and Future Trends
1. **Material Preparation:** The process begins with the sourcing of high-quality stainless steel coils, which are cut to appropriate lengths. The choice of stainless steel grade—such as 304, 316, or duplex stainless steel—depends on the specific application for which the pipes are intended.
2. **Forming:** The prepared steel strips are fed into forming equipment, which shapes them into a tubular form. This is usually accomplished through processes like roll forming or welding. In the case of welded pipes, the edges of the strips are heated and fused together to create a solid seam.
3. **Welding:** In the welding phase, methods such as TIG (Tungsten Inert Gas) or plasma welding are employed to ensure a strong, leak-proof joint. High-frequency induction welding is also frequently used in modern mills due to its efficiency and precision.
4. **Sizing and Straightening:** Once welded, the pipes are passed through sizing mills to achieve the desired diameter and wall thickness. This stage often involves straightening processes to eliminate any distortion caused during welding.
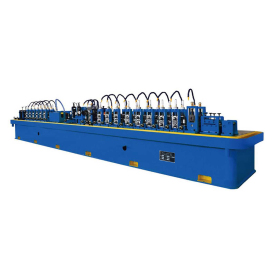
An In-Depth Exploration of the Stainless Steel Pipe Mill Production Line: Innovations, Techniques, and Future Trends
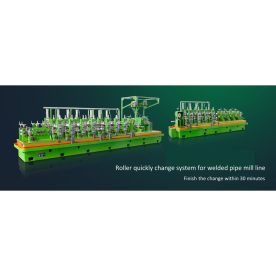
An In-Depth Exploration of the Stainless Steel Pipe Mill Production Line: Innovations, Techniques, and Future Trends
6. **Finishing:** Finally, the pipes are subjected to various finishing processes, such as pickling, passivation, and polishing. These steps enhance the pipes' surface quality, ensuring they meet industry standards and customer expectations.
**Innovations in Stainless Steel Pipe Mill Production Line**
Technological advancements have significantly transformed stainless steel pipe production. Several innovations have emerged in recent years that enhance efficiency, quality, and sustainability, including:
- **Automation:** Many modern stainless steel pipe mills have embraced automation, incorporating advanced robotics and AI-driven systems to streamline operations. This not only reduces labor costs but also improves precision and minimizes human errors.
- **Real-time Monitoring:** The integration of IoT (Internet of Things) technologies allows for real-time monitoring of production processes. Sensors placed throughout the production line provide data on temperature, pressure, and weld integrity, enabling immediate adjustments to optimize quality.
- **Energy Efficiency:** Manufacturers are increasingly focusing on energy-efficient practices. New technologies that reduce energy consumption during production are being implemented, such as high-efficiency motors and heat recovery systems.
- **Sustainability Initiatives:** As environmental concerns rise, stainless steel manufacturers are adopting sustainable practices, including recycling scrap metal and using eco-friendly materials for packaging.
**Challenges Facing the Industry**
Despite the advancements, the stainless steel pipe mill production line faces several challenges:
- **Raw Material Costs:** Fluctuations in the prices of stainless steel can significantly impact production costs. Manufacturers must find ways to mitigate these risks through strategic sourcing and cost management.
- **Global Competition:** As global competition intensifies, manufacturers need to continually innovate to maintain their market position. This might involve investing in new technologies or diversifying product offerings.
- **Environmental Regulations:** Stricter environmental regulations require manufacturers to adapt their processes to minimize their ecological footprint without compromising product quality.
**Future Trends in Stainless Steel Pipe Production**
Looking forward, the stainless steel pipe industry is likely to witness further innovations. Emerging trends may include:
- **Digital Twin Technology:** This technology allows manufacturers to create virtual replicas of their production lines, enabling them to simulate processes, predict failures, and optimize operations.
- **Custom Manufacturing:** With increasing demand for customized solutions, the production of bespoke stainless steel pipes tailored to specific applications will likely become more prevalent.
- **Collaborative Robotics:** The use of collaborative robots (cobots) that work alongside human operators could enhance flexibility and efficiency in the production line.
**Conclusion**
The stainless steel pipe mill production line is essential to satisfying the growing demand for high-quality pipes across various industries. While the sector faces challenges, ongoing innovations and a focus on sustainability promise a bright future for stainless steel pipe manufacturing. As the industry continues to evolve, manufacturers who adapt to technological advancements and market demands will likely thrive in this competitive landscape.