[Durable Spare Parts for Tube Mills]Ensuring Efficiency in Production: The Importance of Durable Spare Parts for Tube Mills in Modern Manufacturing
News 2025-1-16
****In the fast-paced world of manufacturing, tube mills play a critical role in producing high-quality steel and metal tubes used in various industries, from automotive to construction. However, to maintain efficiency and reduce downtime, manufacturers must invest in durable spare parts for tube mills. This article will explore the significance of high-quality spare components, the common types of parts that require regular replacement, and best practices for sourcing these essential items.
Understanding Tube Mills
Tube mills are specialized machines designed to manufacture tubular products by forming flat metal strips into cylindrical shapes. These machines often operate at high speeds and are subjected to significant wear and tear due to the constant friction and pressure during the forming process. Consequently, the performance of tube mills heavily depends on the quality and durability of spare parts used for maintenance and repairs.
The Importance of Durable Spare Parts
1. **Minimizing Downtime**: One of the most significant costs associated with manufacturing is downtime due to equipment failure. Investing in durable spare parts for tube mills can drastically reduce the frequency and duration of such downtimes. Reliable parts ensure that machines operate smoothly, contributing to consistent production levels and allowing manufacturers to meet delivery deadlines more effectively.
2. **Enhancing Product Quality**: The quality of spare parts directly impacts the overall quality of the end product. Durable components help maintain precise tolerances and consistent production standards, which are critical in industries where product specifications are stringent. Using subpar spare parts can lead to defects in the final product, which may result in expensive rework or rejection of entire batches.
3. **Cost Efficiency**: While cheaper spare parts may seem like an attractive option in the short term, they can lead to greater costs over time due to increased wear, decreased lifespan, and a higher likelihood of failure. Quality and durable spare parts often provide a better return on investment, as they reduce replacement frequency and extend the overall lifespan of the equipment.
4. **Safety Considerations**: The safety of workers is paramount in any manufacturing setup. Using durable spare parts helps ensure that the machinery operates safely and reliably, thus minimizing the risk of accidents that could arise from equipment malfunction. Reliable components contribute to an overall safer working environment.
Common Spare Parts for Tube Mills
Manufacturers will encounter several types of parts that regularly require attention and replacement. Understanding these components can help in planning maintenance and ensuring that durable alternatives are always available:
- **Rolls and Die Faces**: These components are subject to the most stress and wear. Durable rolls and die faces made from high-quality materials can withstand the significant deformation forces encountered in tube production.
- **Bearings and Shafts**: Critical for the smooth operation of tube mills, bearings and shafts experience considerable wear. Choosing durable options designed for high-load performance is essential for long-term reliability.
- **Seals and Gaskets**: Preventing leaks and maintaining operational integrity, high-quality seals and gaskets ensure that lubrication remains in place, extending the life of other components.
- **Drive Elements**: Chains, pulleys, and gears are pivotal to the operation of tube mills. Durable drive elements reduce the risk of mechanical failure and improve overall efficiency.
Best Practices for Sourcing Durable Spare Parts
To ensure that tube mills continue to operate at optimal levels, manufacturers should adopt the following best practices when sourcing spare parts:
1. **Research Suppliers**: Take the time to research and evaluate suppliers who specialize in spare parts for tube mills. Look for companies that have a good reputation for quality and service.
2. **Prioritize OEM Parts**: Whenever possible, use Original Equipment Manufacturer (OEM) parts. OEM components are designed specifically for the machine, ensuring better fit and performance compared to aftermarket alternatives.
3. **Consider Quality Certifications**: Check if the suppliers have quality management certifications, such as ISO 9001, which indicate adherence to strict quality control processes.
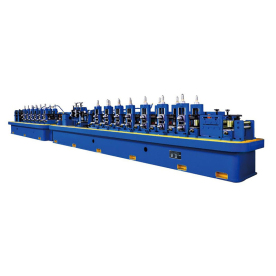
Ensuring Efficiency in Production: The Importance of Durable Spare Parts for Tube Mills in Modern Manufacturing
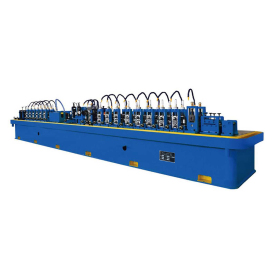
Ensuring Efficiency in Production: The Importance of Durable Spare Parts for Tube Mills in Modern Manufacturing
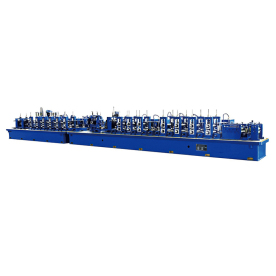
Ensuring Efficiency in Production: The Importance of Durable Spare Parts for Tube Mills in Modern Manufacturing
In conclusion, the importance of durable spare parts for tube mills cannot be overstated. Investing in high-quality components leads to reduced downtime, improved product quality, enhanced safety, and long-term cost savings. Manufacturers must prioritize sourcing durable spare parts to ensure the efficient operation of their tube mills, ultimately contributing to a more robust and resilient manufacturing process that meets the demands of today's industries. With careful planning and attention to quality, tube mill operators can maintain their competitive edge in the market.