[Industrial tube making machinery]Exploring the Evolution, Applications, and Future of Industrial Tube Making Machinery in Modern Manufacturing Processes
News 2025-1-16
Industrial tube making machinery has undergone significant advancements over the years, evolving from simplistic manual operations to sophisticated automated systems that play a critical role in various manufacturing sectors. The production of tubes and pipes is integral to a multitude of industries, including construction, automotive, aerospace, and chemical processing. Given the omnipresence of tubes in our daily lives, understanding the evolution and current landscape of industrial tube making machinery is essential.
The history of tube manufacturing can be traced back to the necessity of creating conduits for fluid transportation. Traditionally, metals or materials were manually shaped into tubes, leading to inconsistencies in quality and performance. The introduction of industrial tube making machinery in the late 19th and early 20th centuries revolutionized the process. These machines enabled manufacturers to produce tubes at a much larger scale, improving not only efficiency but also the standardization of products.
Today, industrial tube making machinery encompasses a variety of machines designed for distinct processes such as welding, bending, cutting, and finishing. Automatic tube mills, for instance, use advanced technology to manufacture tubes from coiled metal sheets. These machines can achieve production speeds that were previously unimaginable, drastically reducing lead times and labor costs. Moreover, the precision of automated machinery means that tubes can be produced to meet specific dimensional and geometric tolerances, ensuring their suitability for various applications.
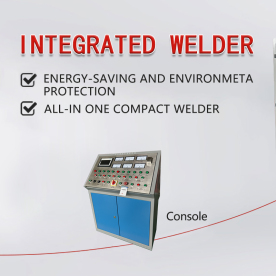
Exploring the Evolution, Applications, and Future of Industrial Tube Making Machinery in Modern Manufacturing Processes
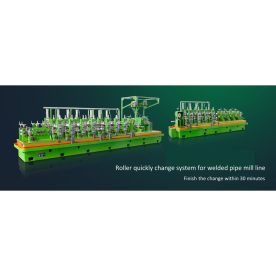
Exploring the Evolution, Applications, and Future of Industrial Tube Making Machinery in Modern Manufacturing Processes
Industrial tube making machinery also prioritizes sustainability and efficiency. Many manufacturers are now investing in energy-efficient models that reduce consumption without sacrificing output. Innovations such as regenerative braking and servo motor technology have proven effective in minimizing energy use during operation. Additionally, the utilization of advanced monitoring systems allows for real-time analysis of production processes, enabling manufacturers to identify inefficiencies and implement improvements.

Exploring the Evolution, Applications, and Future of Industrial Tube Making Machinery in Modern Manufacturing Processes
The application of industrial tube making machinery continues to expand as industries evolve and demand for specialized tubing solutions increases. Innovations such as additive manufacturing and smart technology are on the horizon, potentially transforming how tubes are designed and produced. These technologies open up exciting possibilities for customization and rapid prototyping, allowing manufacturers to respond quickly to changing market demands.
In conclusion, industrial tube making machinery has fundamentally transformed the manufacturing landscape, enabling efficient, cost-effective, and high-quality production of tubes across diverse sectors. As technology continues to advance, the future of tube making promises to be even more dynamic and innovative. With a focus on sustainability, adaptability, and safety, modern tube making machinery is set to play a pivotal role in shaping future manufacturing processes while meeting the ever-changing needs of industries worldwide.