[High frequency welder]Understanding the Benefits and Applications of High Frequency Welders in the Manufacturing Industry
News 2025-1-14
High-frequency welding is a specialized technique essential in various sectors of manufacturing, predominantly used to fuse plastic materials and thin sheets of metal. The technology revolves around the principle of generating high-frequency electromagnetic fields to create heat in the materials to be joined, allowing for a quick and efficient welding process. This article delves into the benefits and various applications of high-frequency welders, highlighting their significance in modern manufacturing.
What is High-Frequency Welding?
High-frequency welding, also known as radio frequency (RF) welding, utilizes electromagnetic waves within a frequency range of 3 to 300 MHz. When these waves pass through dielectric materials, they generate heat due to molecular friction. This heat allows the materials to melt at their joints, creating a strong bond once cooled. The process is particularly effective for materials like thermoplastics and is widely used in industries such as automotive, aerospace, medical, and packaging.
Advantages of High-Frequency Welders
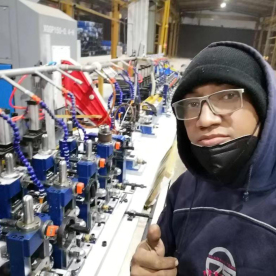
Understanding the Benefits and Applications of High Frequency Welders in the Manufacturing Industry
**2. Strong and Durable Welds:** The welds created through high-frequency welding are known for their exceptional strength and durability. The method ensures a seamless bond, often enhancing the material's integrity rather than compromising it. This is crucial in applications where the welded joints must endure significant stress or pressure.
**3. Versatility:** High-frequency welders can be utilized on a wide range of materials, including vinyl, PVC, polyurethane, and other thermoplastics, making them a versatile tool in any manufacturing setup. Additionally, they can bond various shapes and sizes, from flat sheets to complex geometries, allowing for diverse product designs.
**4. Clean and Precise:** Unlike traditional welding methods, which may incorporate various additional materials or generate significant waste, high-frequency welding requires minimal cleaning and setup. The process produces clean edges without excessive burn marks or residues, ensuring a high-quality aesthetic and functional outcome.
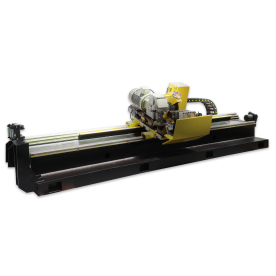
Understanding the Benefits and Applications of High Frequency Welders in the Manufacturing Industry
Applications of High-Frequency Welders
**1. Automotive Industry:** High-frequency welders are prominently used in the automotive sector for creating seam welds in plastic components, such as dashboards, panels, and fuel tanks. The process ensures the components are lightweight yet strong, contributing to the overall efficiency and performance of vehicles.
**2. Medical Devices:** In the medical field, high-frequency welding is used to create sterile, leak-proof seals in products such as IV bags, tubing, and hospital gowns. This reliable sealing is critical in ensuring the safety and longevity of medical supplies.
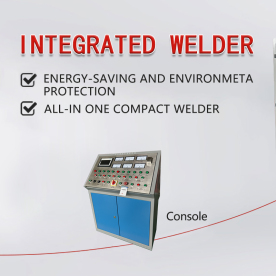
Understanding the Benefits and Applications of High Frequency Welders in the Manufacturing Industry
**4. Packaging Solutions:** High-frequency welding is widely used in the packaging industry to create bags and containers, especially those made from plastic and laminates. This method enhances the durability of packages, reduces leakage, and ensures that containers are food-safe.
Conclusion
High-frequency welders have transformed many aspects of the manufacturing process, providing significant advantages in terms of speed, efficiency, and quality. Their versatility ensures they are indispensable in various industries, from automotive to medical devices. As the manufacturing landscape continues to evolve, the role of high-frequency welding is likely to expand, paving the way for innovative techniques and applications. By embracing this technology, businesses can not only improve their production capabilities but also enhance the quality of their products, positioning themselves competitively in the market.