[Reliable Annealing Machine Replacement Components]Ensure Optimal Performance with Reliable Annealing Machine Replacement Components: A Comprehensive Guide for Industry Professionals
News 2025-1-14
****In the world of industrial machinery, one of the most critical components for achieving high-quality manufacturing output is the annealing machine. This specialized equipment plays a vital role in the metalworking and glass industries, providing necessary heat treatment processes to modify material properties for enhanced performance. However, as with any machinery, wear and tear can lead to the need for reliable annealing machine replacement components. This article delves into the importance of utilizing dependable replacement parts, how to identify quality components, and the best practices for maintaining your annealing machines.
Understanding Annealing Machines
Annealing machines are designed to heat materials to a specific temperature and then allow them to cool down gradually. This process relaxes internal stresses, improves ductility, and alters mechanical properties in metals and glass. Industries such as automotive, aerospace, and construction rely heavily on the reliable performance of these machines to maintain product integrity and compliance with industry standards.
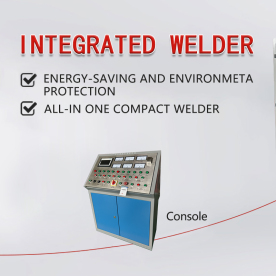
Ensure Optimal Performance with Reliable Annealing Machine Replacement Components: A Comprehensive Guide for Industry Professionals
The intense operating conditions under which annealing machines function can lead to component degradation over time. Key parts such as heating elements, temperature sensors, conveyor systems, and control panels can become less effective or fail entirely. Using unreliable or substandard replacement components can lead to numerous issues, including:
1. **Decreased Efficiency**: Poor-quality components may not function optimally, causing delays in production and increased energy consumption. 2. **Inconsistent Results**: The quality of the annealing process relies heavily on precise temperature control and uniform heating. Inconsistent components can lead to variations in product quality, affecting customer satisfaction and leading to costly rework or scrap. 3. **Increased Downtime**: There’s nothing worse than unexpected machine downtime due to component failures. Reliable replacement parts significantly reduce the likelihood of malfunctions, ensuring smoother continuity in production schedules. 4. **Safety Hazards**: Faulty components can pose serious safety risks, leading to potential accidents or injuries in the workplace. Using quality replacement parts minimizes these risks substantially.
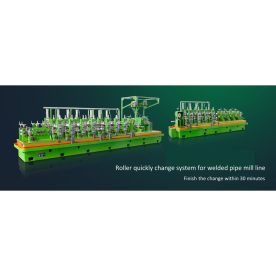
Ensure Optimal Performance with Reliable Annealing Machine Replacement Components: A Comprehensive Guide for Industry Professionals
When it comes to sourcing replacement components for your annealing machines, it’s essential to ensure that they are reliable and meet the necessary specifications. Here are some guidelines to help you identify high-quality parts:
1. **OEM vs. Aftermarket**: Original Equipment Manufacturer (OEM) parts are designed specifically for your machine and are typically the safest choice. Aftermarket parts may offer cost savings, but they could lack the same level of quality and compatibility. 2. **Certifications and Standards**: Always check if the parts meet industry standards and certifications. This ensures their reliability and effectiveness in performance. 3. **Manufacturer Reputation**: Research manufacturers and suppliers thoroughly. Look for companies with a solid reputation in the market, backed by positive customer reviews and case studies.
4. **Testing and Quality Assurance**: Ensure that the components have undergone rigorous testing and adhere to quality assurance protocols. This is particularly crucial for critical components such as temperature sensors and heating elements.
Best Practices for Maintaining Annealing Machines
To extend the lifespan of your annealing machines and their components, regular maintenance is crucial. Here are a few best practices:
1. **Scheduled Inspections**: Implement a routine inspection schedule to identify any wear or damage before it leads to failure. This proactive approach can save time and costs in the long run. 2. **Proper Training**: Ensure that operators are adequately trained to use and maintain the equipment. Knowledgeable personnel can identify potential issues and take corrective action before problems escalate. 3. **Document Maintenance**: Keep accurate records of all maintenance activities and parts replacements. This information can be invaluable for tracking the performance of specific components and for planning future replacements.
4. **Upgrade When Necessary**: As technology advances, consider upgrading to newer components that offer improved efficiency and performance. While this may involve an upfront cost, the long-term benefits usually outweigh the initial investment.
Conclusion
