[Stainless steel Tube making machine]Understanding the Advantages and Applications of Stainless Steel Tube Making Machines in Modern Manufacturing
News 2025-1-14
In the rapidly evolving world of manufacturing, stainless steel has carved out a significant niche due to its durability, corrosion resistance, and versatile applications across various industries. At the heart of producing high-quality stainless steel products is the stainless steel tube making machine, a vital piece of equipment that streamlines the creation of seamless and welded tubes for diverse applications. This article delves into the advantages of using these machines, their operational mechanisms, and their significance in contemporary manufacturing processes.
**The Importance of Stainless Steel Tubes**
Stainless steel tubes are essential components in several industries, including construction, automotive, aerospace, and healthcare. Their resistance to rust and staining, coupled with high-temperature tolerance, makes them ideal for use in environments exposed to harsh conditions. As industries evolve, the demand for specialized stainless steel tubes—such as those required for thermal management systems, exhaust systems, and surgical instruments—has increased. This surge in demand necessitates high-efficiency manufacturing processes, highlighting the crucial role of stainless steel tube making machines.
**Types of Stainless Steel Tube Making Machines**
Stainless steel tube making machines typically fall into two categories: seamless and welded tube-making machines.
1. **Seamless Tube Making Machines**: These machines utilize advanced techniques such as rotary piercing and elongation processes to manufacture tubes without any seams. The seamless tubes produced are often used in high-pressure applications, such as oil and gas pipelines, due to their structural integrity and ability to withstand significant stress.
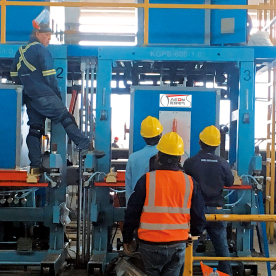
Understanding the Advantages and Applications of Stainless Steel Tube Making Machines in Modern Manufacturing
**Advantages of Stainless Steel Tube Making Machines**
Stainless steel tube making machines offer several advantages that enhance manufacturing efficiency and product quality.
1. **High Production Efficiency**: These machines are designed for mass production, significantly reducing cycle times while maintaining high levels of accuracy. Automation features, such as computerized controls and robotics, enable manufacturers to operate these machines with minimal human intervention, thus increasing productivity.
2. **Material Savings**: Advanced tube making machines maximize the use of raw materials, minimizing waste. Technologies such as laser cutting and precise welding techniques allow manufacturers to produce tubes with the desired dimensions while using less stainless steel than traditional methods.
3. **Quality Control**: Modern stainless steel tube making machines often incorporate various quality control mechanisms, such as non-destructive testing and on-line measurement systems. This ensures that the finished products meet stringent industry standards and customer specifications, thus enhancing customer satisfaction and reducing the likelihood of returns.
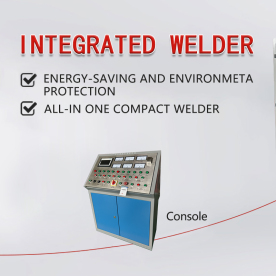
Understanding the Advantages and Applications of Stainless Steel Tube Making Machines in Modern Manufacturing
5. **Reduced Labor Costs**: As manufacturers transition to more automated solutions, the dependence on manual labor significantly decreases. Stainless steel tube making machines require fewer operators, leading to reduced labor costs while enhancing safety in the workplace.
**Applications Across Industries**
The applications of stainless steel tubes are broad and varied. In the *automotive industry*, they are used in exhaust systems, fuel lines, and structural components. The *aerospace sector* utilizes stainless steel tubes in hydraulic systems and airframe structures due to their strength-to-weight ratio. Additionally, the *construction industry* employs these tubes in architectural frameworks and piping systems for water, gas, and air.
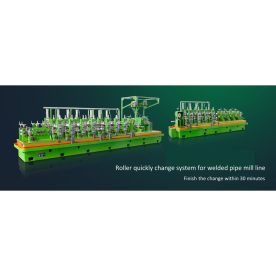
Understanding the Advantages and Applications of Stainless Steel Tube Making Machines in Modern Manufacturing
**Conclusion**
In summary, stainless steel tube making machines are essential in modern manufacturing, offering increased efficiency, versatility, and quality control. Their contributions to producing high-quality stainless steel tubes have widespread implications across multiple industries, ensuring that manufacturers can meet the growing demands of the market while maintaining competitive advantages. As technology continues to advance, we can anticipate further enhancements in stainless steel tube making processes, paving the way for even greater innovations in the future.